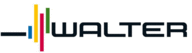
Catalog excerpts
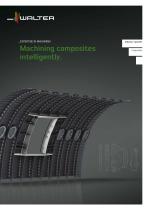
Machining composites intelligently.
Open the catalog to page 1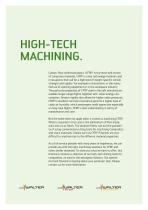
HIGH-TECH MACHINING. Carbon-fibre reinforced plastic (CFRP) is the most well-known of composite materials. CFRP is a key technology material used in situations that call for a high level of weight-specific tensile strength and rigidity: For example in Automotive, in the manufacture of sporting equipment or in the aerospace industry. The particular properties of CFRP used in Aircraft manufacture enables longer range flights together with lower energy consumption. Greater rigidity also allows for higher cabin pressures. CFRP's excellent corrosion resistance permits a higher level of cabin...
Open the catalog to page 2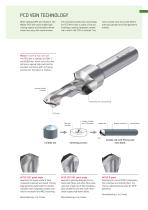
PCD VEIN TECHNOLOGY When drilling CFRP and titanium, the Walter PCD Vein tools enable high cutting speeds and excellent dimensional accuracy with minimal wear. The innovative production technology for PCD Vein tools is state of the art. Including a special designed carbide nib in which the PCD is sintered. The nib is brazed onto the shank before precision grinded and final geometry eroded. Walter Titex PCD Vein rivet drill The PCD Vein is sintered at 1500 °C and 60,000 bar, which turns this rivet drill into a special high-tech tool for excellent machining with no fraying and low burr...
Open the catalog to page 3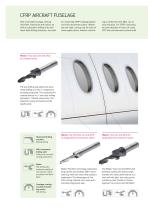
CFRP AIRCRAFT FUSELAGE CNC-controlled fuselage riveting machines, flextracks and robots, as well as automatic drilling units and hand-held drilling machines, are used for machining CFRP fuselage panels and their attachment parts. Walter has the right cutting tool for each of these applications, whether machin- ing is performed with MQL, dry or with emulsion. For CFRP machining, we have decided in favour of using PCD Vein and diamond-coated solid Walter Titex PCD Vein rivet drill AF3P for longitudinal and transverse seams Walter Titex rivet drill AF1D for l ongitudinal and transverse seams...
Open the catalog to page 4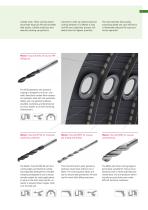
matched in order to achieve optimum coating adhesion. For Walter a long tool life and, especially, process reliability have the highest priorities. The ratio between hole quality, m achining speed and cost efficiency is individually adjusted for each particular operation. Walter Titex drill AFF1D for moderate machining conditions Walter Titex drill MFF1 for manual pre-drilling and drilling Walter Titex drill MFA1 for manual counterboring The Walter Titex drill AFF1D with four cutting edges and diamond coating was especially developed for unstable clamping arrangements and is exceptionally...
Open the catalog to page 5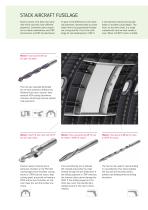
STACK AIRCRAFT FUSELAGE Stacks consist of at least two materials which may each have different properties. Commonly used composite-to-metal combinations are CFRP and titanium or CFRP and aluminium. In spite of the difference in the material properties, dimensionally accurate holes have to be guaranteed throughout a long tool life. That is the challenge for tool development. CFRP is a very abrasive material and quickly leads to rounded cutting edges. Titanium, on the other hand, is a tough material with very low heat conductance. When a CFRP/Ti stack is drilled, Walter Titex PCD Vein rivet...
Open the catalog to page 6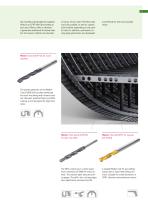
the rounded cutting edge has negative effects on CFRP like fibre breakouts and uncut fibres, while in titanium, it generates additional frictional heat. For that reason, Walter has decided in favour of low-wear PCD Vein tools and solid carbide, as well as coated solid carbide, depending on the task at hand. In addition, optimised cutting edge geometries are developed and offered for the best possible result. Walter Titex drill AFT3A for stack material Floorgrid image The proven geometry of the Walter Titex A3366 drill has been perfected for stack machining with internal coolant channels,...
Open the catalog to page 7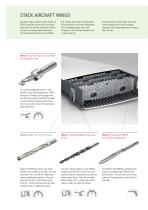
STACK AIRCRAFT WINGS ent stacks also varies considerably. From hole sizes of a few millimetres for the leading edge outer skin through to 15 x d holes towards the centre wing box. The diameters of the holes also vary more sharply than in the fuselage segment and reach diameters of more than 30 mm. Walter B4017 Point Drill for drilling Walter Titex drill AFA1N for wing spar to ribs Walter Titex step drill MFA5 for manual counterboring Ideal for CFRP/aluminium one-shotdrilling. Cost-effective solution for hole diameters of 12 to 38 mm. Maximum process reliability thanks to the optimised drill...
Open the catalog to page 8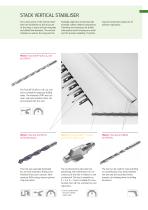
STACK VERTICAL STABILISER fuselage segments are dynamically stressed, safety-related components. Therefore the tolerances for drilled hole quality result in being very small and the process reliability of machin- ing and component quality are of primary importance. Walter Titex step drill AFT1A forTi/steel stacks Walter Prototyp ConeFit* counter sinker for Ti, steel and Al Walter Titex step drill MFA4 for CFRP/Al This tool was especially developed for use with automatic drilling units. Polished flutes and a smooth, heatresistant ACN coating ensure optimal chip evacuation. The...
Open the catalog to page 9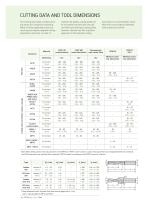
CUTTING DATA AND TOOL DIMENSIONS The cutting data table contains starting values for composite machining. Many of these applications are nonrecurring and require adapted cutting parameters and tools. In order to improve hole quality, cutting speed can be increased and feed rate reduced. Low feed rate and high cutting speed, however, shorten tool life. A gradual approach to find optimal cutting p arameters is recommended, which allow the correct balance between hole quality and tool life. Thermoplastic with carbon fibre CFRP/Ti Al/Ti Minimum quan tity lubrication Minimum quan tity...
Open the catalog to page 10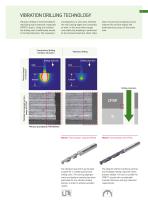
VIBRATION DRILLING TECHNOLOGY Vibration drilling is recommended for machining stack materials, especially CFRP/Ti stacks. Using this method, the drilling tool is additionally moved in the feed direction. The movement corresponds to a sine wave, whereby the tool cutting edges are constantly at work. In the sinus wave trough, controlled chip breaking is performed at the minimum feed rate. Short chips Conventional drilling (without vibration) Vibration drilling Drilling direction Drilling direction Drill Thermal image of titanium lower the process temperature and improve the surface quality...
Open the catalog to page 11All WALTER FRANCE catalogs and technical brochures
-
Product highlights 2019
132 Pages
-
Product Innovations catalogue
700 Pages
-
AEROSPACE Fuselages
4 Pages
-
AEROSPACE Engines
4 Pages
-
AEROSPACE landing gears
4 Pages
-
GLOBALLY UNIQUE
12 Pages
-
THE MACHINING AGE IS OVER
84 Pages
-
Tiger tec Silber Turning
60 Pages
-
Go for better, go for Gold.
276 Pages
-
Engines
4 Pages
-
Fuselages
4 Pages
-
landing gears
4 Pages