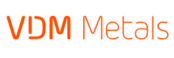

Catalog excerpts
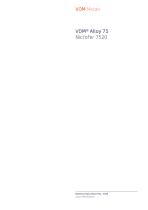
Material Data Sheet No. 4035 June 1994 Edition
Open the catalog to page 1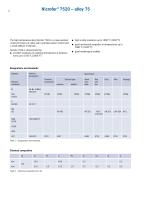
The high-temperature alloy Nicrofer 7520 is a creep-resistant nickel-chromium-iron alloy with controlled carbon content and a small addition of titanium. Nicrofer 7520 is characterized by: • excellent resistance to oxidizing atmospheres at temperatures up to 1100 °C (2000 °F) • high scaling resistance up to 1000 °C (1830 °F) • good mechanical properties at temperatures up to 1000 °C (1830 °F) • good metallurgical stability Table 1 - Designations and standards. Table 2 - Chemical composition (wt.-%).
Open the catalog to page 2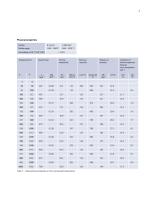
Table 3 - Typical physical properties at room and elevated temperatures.
Open the catalog to page 3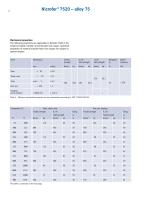
Mechanical properties The following properties are applicable to Nicrofer 7520 in the solution-treated condition and indicated size ranges. Specified properties of material outside these size ranges are subject to special enquiry. This table is continued on the next page.
Open the catalog to page 4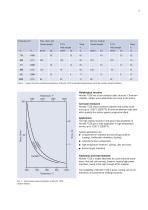
Table 5 - Typical short-time mechanical properties of Nicrofer 7520 at elevated temperatures and in the solution-treated condition. Metallurgical structure Nicrofer 7520 has a face-centered cubic structure. Chromium carbides, nitrides and carbonitrides can occur in the matrix. Corrosion resistance Nicrofer 7520 shows excellent oxidation and scaling resistance up to 1100 °C (2000 °F). It forms an adherent oxide layer which protects the surface against progressive attack. Applications The high scaling resistance and good creep properties of Nicrofer 7520 give it wide application in high...
Open the catalog to page 5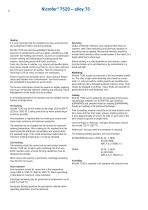
Heating It is very important that the workpiece be clean and free from any contaminant before and during heating. Nicrofer 7520 may become embrittled if heated in the presence of contaminants such as sulphur, phosphorus, lead and other low-melting-point metals. Sources of contamination include marking and temperature-indicating paints and crayons, lubricating grease and fluids, and fuels. Fuels must be low in sulphur; e.g. natural and liquefied petroleum gases should contain less than 0.1 % by mass and town gas 0.25 g/m3 maximum of sulphur. Fuel oils containing no more than 0.5% by mass of...
Open the catalog to page 6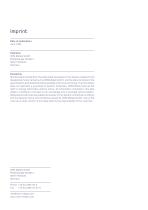
Imprint Date of publication June 1994 Publisher VDM Metals GmbH Plettenberger Straße 2 58791 Werdohl Germany Disclaimer All information contained in this data sheet are based on the results of research and development work carried out by VDM Metals GmbH, and the data contained in the specifications and standards listed available at the time of printing. The information does not represent a guarantee of specific properties. VDM Metals reserves the right to change information without notice. All information contained in this data sheet is compiled to the best of our knowledge and is provided...
Open the catalog to page 7All VDM METALS GMBH catalogs and technical brochures
-
Powder
12 Pages
-
Exhaust Gas Cleaning
20 Pages
-
Chemical Process Industry
32 Pages
-
Flue Gas Desulfu– rization
28 Pages
-
The world of VDM Metals
5 Pages
-
VDM® Powder 718
5 Pages
-
VDM® Alloy 36
13 Pages
-
VDM® Powder X
5 Pages
-
VDM® Alloy X-750
16 Pages
-
VDM® Alloy 188
8 Pages
-
VDM® Powder 780
5 Pages
-
VDM Metals Materials Catalog
28 Pages
-
VDM® Alloy 718
13 Pages