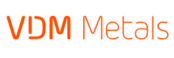

Catalog excerpts
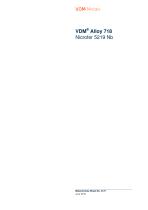
VDM® Alloy 718 Nicrofer 5219 Nb Material Data Sheet No. 4127 June 2016
Open the catalog to page 1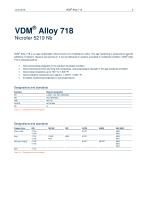
June 2016 VDM® Alloy 718 2 VDM® Alloy 718 is an age hardenable nickel-chrome-iron-molybdenum alloy. The age hardening is achieved by specific additions of niobium, titanium and aluminum. It can be delivered in solution-annealed or hardened condition. VDM® Alloy 718 is characterized by: • Good processing properties in the solution-annealed condition • Good mechanical short and long-term properties, and great fatigue strength in the age hardened condition • Good creep resistance up to 700 °C (1,300 °F) • Good oxidation resistance up to approx. 1,000°C (1,830 °F) • Excellent mechanical...
Open the catalog to page 2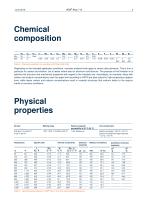
June 2016 VDM® Alloy 718 3 Chemical composition ppm ppm ppm Table 2 - Chemical composition (%) according to ASTM and SAE AMS Depending on the intended application conditions, narrower analysis limits apply to certain alloy elements. This is true in particular for carbon and niobium, but to lesser extent also for aluminum and titanium. The purpose of this limitation is to optimize the structure and mechanical properties with regard to the intended use. Accordingly, for example, alloys with carbon and niobium concentrations near the upper limit according to ASTM are best suited for...
Open the catalog to page 3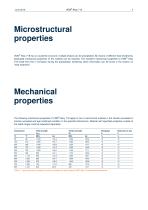
June 2016 VDM® Alloy 718 4 VDM® Alloy 718 has an austenitic structure; multiple phases can be precipitated. By means of different heat treatments, graduated mechanical properties of the material can be reached. The excellent mechanical properties of VDM® Alloy 718 result from the Y”-formation during the precipitation hardening. More information can be found in the section on “heat treatment”. The following mechanical properties of VDM® Alloy 718 apply to hot or cold-formed material in the solution-annealed or solution-annealed and age hardened condition in the specified dimensions. Material...
Open the catalog to page 4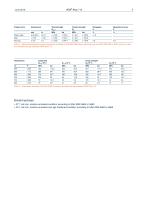
June 2016 VDM® Alloy 718 5 Product form Dimensions Yield strength Tensile strength Elongation Reduction of area Table 5 - Mechanical properties at room temperature according to SAE AMS 5596 (sheet, plate and strip) and SAE AMS 5662 or 5663 (rod, bar) of solution-annealed and age hardened VDM® Alloy 718 Temperature Creep limit Creep strength Table 6 - Creep limits according to DIN EN 10302 of solution-annealed and age hardened VDM® Alloy 718
Open the catalog to page 5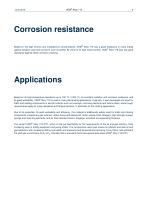
Based on the high chrome and molybdenum concentrations, VDM Alloy 718 has a good resistance in many media ® against abrasive and local corrosion such as pitting. By virtue of its high nickel content, VDM Alloy 718 also has good resistance against stress corrosion cracking. Applications Based on its high-temperature resistance up to 700 °C (1,300 °F), its excellent oxidation and corrosion resistance, and ® its good workability, VDM Alloy 718 is used in many demanding applications. Originally, it was developed and used for static and rotating components in aircraft turbines such as housings,...
Open the catalog to page 6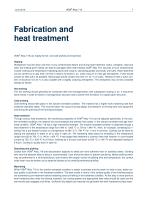
Fabrication and heat treatment ® VDM Alloy 718 can readily be hot- and cold-worked and machined. Heating Workpieces must be clean and free of any contaminants before and during heat treatment. Sulfur, phosphor, lead and ® other low-melting-point metals can lead to damages when heat treating VDM Alloy 718. Sources of such contaminants include marking and temperature-indicating paints and crayons, lubricating grease and fluids, and fuels. Heat treatments can be carried out in gas fired, oil fired or electric furnaces in air, under vacuum or inert gas atmosphere. Fuels should contain as little...
Open the catalog to page 7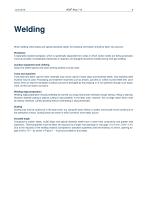
Welding When welding nickel alloys and special stainless steels, the following information should be taken into account: Workplace A separately located workplace, which is specifically separated from areas in which carbon steels are being processed, must be provided. Considerable cleanliness is required, and draughts should be avoided during inert gas welding. Auxiliary equipment and clothing Clean fine leather gloves and clean working clothes must be used. Tools and machines Tools that have been used for other materials may not be used for nickel alloys and stainless steels. Only stainless...
Open the catalog to page 8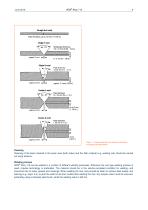
Figure 1 – Seam preparation for welding nickel alloys and special stainless steels. Cleaning Cleaning of the basic material in the seam area (both sides) and the filler material (e.g. welding rod) should be carried out using acetone. Welding process ® VDM Alloy 718 can be welded in a number of different welding processes. Wherever the inert gas welding process is used, impulse technology is preferable. The material should be in the solution-annealed condition for welding, and should be free of scale, grease and markings. When welding the root, care should be taken to achieve best quality...
Open the catalog to page 9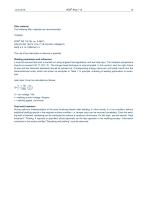
Filler material The following filler materials are recommended: TIG/MIG ® VDM FM 718 (W. no. 2.4667) DIN EN ISO 18274: S Ni 7718 (SG-NiCr19NbMoTi) AWS A 5.14: ERNiFeCr-2 The use of bar electrodes in sleeves is possible. Welding parameters and influences It must be ensured that work is carried out using targeted heat application and low heat input. The interpass temperature should not exceed 100 °C (212 °F). The stringer bead technique is recommended. In this context, also the right choice of wire and bar electrode diameters should be pointed out. Corresponding energy inputs per unit length...
Open the catalog to page 10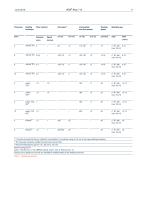
June 2016 VDM® Alloy 718 11 Intermediate Welding Shielding gas and final passes speed (mm) Diameter Speed I in (A) U in (V) I in (A) U in (V) (cm/min) Type Rate 1) It must be ensured that there is sufficient root protection, for example using Ar 4.6, for all inert gas welding processes. 2) The root pass should be welded manually (see manual TIG). 3) Recommended plasma gas Ar 4.6 / rate 3.0 to 3.5 l/min Section energy kJ/cm: autom. TIG HD max. 6, TIG, GMAW manual, autom. max. 8; Plasma max. 10 Figures are for guidance only and are intended to facilitate setting of the welding...
Open the catalog to page 11All VDM METALS GMBH catalogs and technical brochures
-
Powder
12 Pages
-
Exhaust Gas Cleaning
20 Pages
-
Chemical Process Industry
32 Pages
-
Flue Gas Desulfu– rization
28 Pages
-
The world of VDM Metals
5 Pages
-
VDM® Powder 718
5 Pages
-
VDM® Alloy 36
13 Pages
-
VDM® Powder X
5 Pages
-
VDM® Alloy X-750
16 Pages
-
VDM® Alloy 75
7 Pages
-
VDM® Alloy 188
8 Pages
-
VDM® Powder 780
5 Pages
-
VDM Metals Materials Catalog
28 Pages