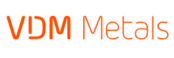

Catalog excerpts
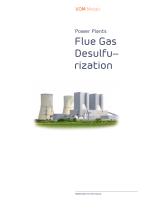
Power Plants Flue Gas Desulfu– rization
Open the catalog to page 1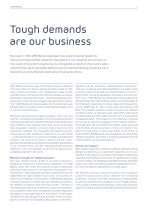
Tough demands are our business Founded in 1930, VDM Metals developed into a world market leader for high-performing metallic materials. The quality of our products and services is the result of long-term experience, our integrated production chain and a sales network that spans the globe. VDM serves the most demanding industries and is backed by a strong R&D and Application Engineering force. VDM Metals produces high-performance nickel, cobalt and zirconium alloys as well as special stainless steels for the use in extreme conditions. Our materials are made to last, resisting heavy...
Open the catalog to page 3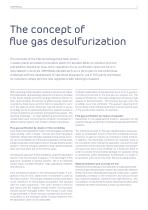
The concept of flue gas desulfurization The principles of the FGD technology have been proven in power plants and waste incineration plants for decades. When air pollution and acid precipitation became an issue, strict regulations for air purification came into force in many Western countries. VDM Metals decided early-on to do its part to overcome these challenges with the development of new alloys designed for use in FGD plants and helped its customers comply with the new regulations with meaningful systems. With a growing world population looking to achieve ever higher living standards,...
Open the catalog to page 5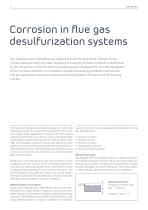
Corrosion in flue gas desulfurization systems The materials used in FGD plants are required first and foremost to be resistant to the, in some cases, extremely corrosive conditions. The severity of these conditions is determined by the composition of the fuel and the scrubbing process employed. For an exact assessment of the corrosive conditions, it is necessary to know all operating parameters like fuel and flue gas composition, operating temperature and the products formed during the cleaning process. The mixture of flue gas and scrubbing suspension, which are intensively brought into...
Open the catalog to page 6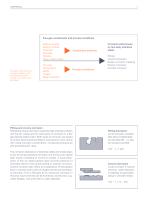
Flue-gas constituents and process conditions, and corrosion phenomena caused on low-alloy stainless steels Flue-gas constituents and process conditions Corrosion phenomena on low-alloy stainless steels Pitting Crevice Corrosion Stress-corrosion cracking Erosion corrosion Contact corrosion Sulphur dioxide Sulphur trioxide Chlorides Fluorides Nitrates Heavy metal oxides pH value Temperature Solids Oxygen Water treatment Pitting and crevice corrosion Pitting and crevice corrosion caused by high chloride contents and low pH values are the main types of corrosion in a flue gas desulfurization...
Open the catalog to page 7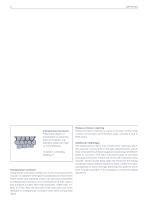
Intergranular Corrosion Preferential attack of precipitations containing grain boundaries, e.g. stainless steels (too high C, not stabilized) f (medium, annealing, welding, T) Intergranular corrosion Intergranular corrosion or attack is a form of corrosion which occurs in or adjacent to the grain boundaries of a metal. Some Nickel alloys and stainless steels may become susceptible to intergranular corrosion as a consequence of their carbon and tungsten content after heat treatment. VDM® Alloy 31, Alloy 31 Plus, Alloy 59 and Alloy 2120 now are much more resistant to intergranular corrosion...
Open the catalog to page 8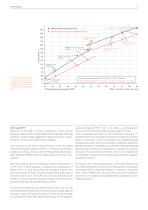
C ritical Crevice Corrosion Temperature CCT Critical Pitting Temperature CPT VDM® Alloy 31 / 31 Plus 1.4562 30 The higher the PRE number of an alloy the higher are the Critical Crevice Corrosion Temperature (CCT) and the Critical Pitting Temperature (CPT) - tainless Steels tested in 10 % FeCl3 x 6 H2O - Solution S - ickel-alloys tested in 7 % H2SO4, 3 % HCl, 1 % CuCl2, 1 % FeCl3. N CCT and CPT Because of the high corrosion resistance of the special stainless steels and the nickel alloys used in flue gas cleaning systems, several highly aggressive tests have been established to compare and...
Open the catalog to page 9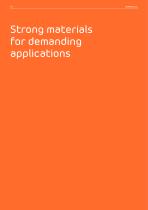
Strong materials for demanding applications
Open the catalog to page 10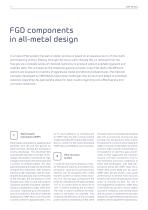
In a typical FGD system, the wet scrubber process is based on an aqueous slurry of lime (CaO) and limestone (CaCO3). Passing through the slurry, sulfur dioxide (SO2) is removed from the flue gas, via a complex series of chemical reactions, to produce calcium sulphate (gypsum) and sulphite salts. This is known as the limestone gypsum process. In any FGD plant, the different sectors are exposed to a variety of aggressive media and altering temperatures. The material concepts developed by VDM Metals take these challenges into account and adapt to individual solutions regarding the appropriate...
Open the catalog to page 11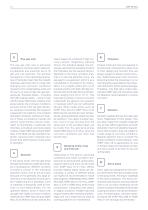
The raw gas inlet area is extremely vulnerable to corrosion due to rebounding absorber and quencher slurry, fly ash and rust particles. The extreme fluctuations in the operating parameters of the boiler mean that the metallic materials used here have to cope with changing wet corrosion conditions caused by the condensating acids and the slurry as well as high raw gas temperatures. Stainless steels – including the 6 Mo special steels – cannot cope with this at all. Particularly in lignite-fired power plants, the corrosion conditions are even worse in the raw gas inlet areas, because of...
Open the catalog to page 12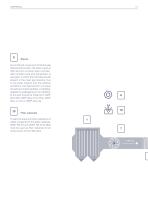
As it is the last component of the flue gas desulfurization plant, the stack is also at high risk from corrosion due to condensate formation and also penetration of rainwater, in which the chlorides are still present in the clean gas dissolve. Due to the great heights and the weather conditions, the head section of a stack should have metal cladding. A cladding, realized by wallpapering or roll-cladding, at this part should be made from VDM ® Alloy 926, VDM ® Alloy 31/31 Plus, VDM ® Alloy C-276 or VDM ® Alloy 59. Filler materials To reach an equal corrosion resistance of welds compared to...
Open the catalog to page 13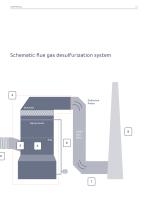
Schematic flue gas esulfurization system d 4 Deflection Plates Demister Spray levels
Open the catalog to page 14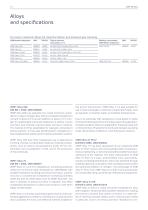
Typical chemical composition, in % VDM® Alloy 926 VDM® Alloy 31 VDM Alloy 31 Plus® VDM® Alloy C-276 VDM® Alloy 59 VDM® Alloy 2120 MoN VDM® Alloy 926 DIN EN 1.4529, UNS N08926 VDM® Alloy 926 is an austenitic iron-nickel-chromium-molybdenum-copper-nitrogen alloy with an increased molybdenum content of about 6.5 % and an addition of about 0.2 % nitrogen for substantially improved resistance to pitting, crevice corrosion and chloride-induced stress-corrosion cracking. The material is firmly established for seawater and product piping systems, for flue-gas desulfurization installations in...
Open the catalog to page 16All VDM METALS GMBH catalogs and technical brochures
-
Powder
12 Pages
-
Exhaust Gas Cleaning
20 Pages
-
Chemical Process Industry
32 Pages
-
The world of VDM Metals
5 Pages
-
VDM® Powder 718
5 Pages
-
VDM® Alloy 36
13 Pages
-
VDM® Powder X
5 Pages
-
VDM® Alloy X-750
16 Pages
-
VDM® Alloy 75
7 Pages
-
VDM® Alloy 188
8 Pages
-
VDM® Powder 780
5 Pages
-
VDM Metals Materials Catalog
28 Pages
-
VDM® Alloy 718
13 Pages