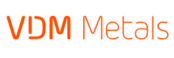

Catalog excerpts
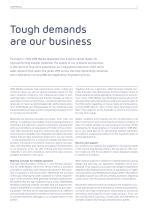
Tough demands are our business Founded in 1930, VDM Metals developed into a world market leader for high-performing metallic materials. The quality of our products and services is the result of long-term experience, our integrated production chain and a sales network that spans the globe. VDM serves the most demanding industries and is backed by a strong R&D and Application Engineering force. VDM Metals produces high-performance nickel, cobalt and zirconium alloys as well as special stainless steels for the use in extreme conditions. Our materials are made to last, resisting heavy...
Open the catalog to page 3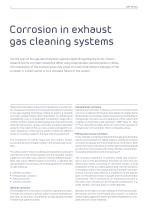
Corrosion in exhaust gas cleaning systems The life span of flue gas desulfurization systems depends significantly on the chosen material and its corrosion resistance. When using inappropriate stainless steels or alloys, the composition of the exhaust gases may cause corrosion that leads to damages of the scrubber in a short period or to a complete failure of the system. Nickel and nickel alloys have proven resistance to a wide variety of aqueous corrosive environments typically encountered in flue gas cleaning technology. Nickel by itself is a versatile corrosion resistant metal. More...
Open the catalog to page 4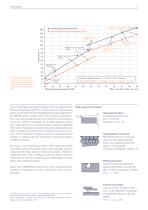
C ritical Crevice Corrosion Temperature CCT Critical Pitting Temperature CPT VDM® Alloy 31 / 31 Plus 1.4562 30 The higher the PRE number of an alloy the higher are the Critical Crevice Corrosion Temperature (CCT) and the Critical Pitting Temperature (CPT) - tainless Steels tested in 10 % FeCl3 x 6 H2O - Solution S - ickel-alloys tested in 7 % H2SO4, 3 % HCl, 1 % CuCl2, 1 % FeCl3. N One of these tests is the determination of the so-called Critical Pitting Temperature (CPT) or Critical Crevice Temperature (CCT) as a function of the Pitting Resistance Equivalent Number (PREN) which is...
Open the catalog to page 5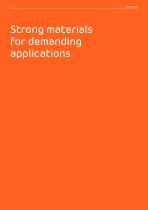
Strong materials for demanding applications
Open the catalog to page 6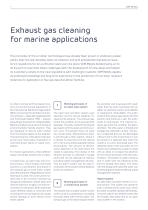
The principles of the scrubber technologies have already been proven in stationary power plants. Over the last decades, when air pollution and acid precipitation became an issue, strict regulations for air purification were put into place. VDM Metals decided early-on to do its part to overcome these challenges with the development of new alloys and helped its customers comply to the new regulations with meaningful systems. VDM Metals applies its extensive knowledge and long-term experience in the production of corrosion resistant materials for application in flue gas desulfurization...
Open the catalog to page 7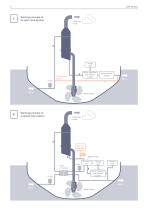
Working principle of an open loop system Sludge tank Water treatment and filtration system Dilution water system Measurement system Water Diesel engine Working principle of a closed loop system Reaction agent tank Heat exchanger Process tank Sludge tank Holding tank Water treatment and filtration system Water Water Diesel engine
Open the catalog to page 8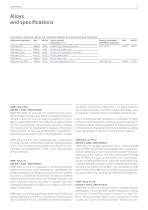
Typical chemical composition, in % VDM® Alloy 926 VDM® Alloy 31 VDM Alloy 31 Plus® VDM® Alloy C-276 VDM® Alloy 59 VDM® Alloy 2120 MoN VDM® Alloy 926 DIN EN 1.4529, UNS N08926 VDM® Alloy 926 is an austenitic iron-nickel-chromium-molybdenum-copper-nitrogen alloy with an increased molybdenum content of about 6.5 % and an addition of about 0.2 % nitrogen for substantially improved resistance to pitting, crevice corrosion and chloride-induced stress-corrosion cracking. The material is firmly established for seawater and product piping systems, for flue-gas desulfurization installations in...
Open the catalog to page 9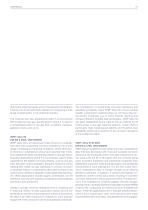
dominantly reducing media, even in the presence of halogens, it has proven to be particularly effective in conquering a wide range of applications in the chemical industry. The material has also established itself in environmental technology like flue gas desulfurization where it is used to a considerable extent in raw gas inlet, scrubbers, dampers, agitators, ducts, and so on. VDM ® Alloy 59 DIN EN 2.4605, UNS N06059 VDM ® Alloy 59 is an advanced nickel-chromium-molybdenum alloy with outstanding corrosion resistance over a wide range of oxidizing and reducing conditions, where other...
Open the catalog to page 10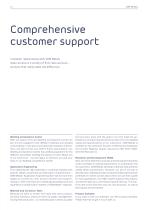
Comprehensive customer support Customer relationships with VDM Metals mean access to a variety of first class services – services that really make the difference. Welding Competence Center With our state-of-the-art Welding Competence Center we are not only capable to test different materials and welding consumables or new and unconventional materials combinations, but also to train your staff in theory and practice. Our Welding Competence Center has welding equipment for the different automated welding processes at hand. Make use of our know-how – we are happy to welcome you and your team...
Open the catalog to page 12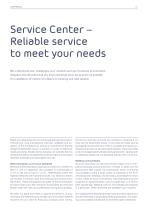
Service Center – Reliable service to meet your needs We understand your challenges, your markets and your business environment. Shipyard retrofit times and dry dock overhauls must be as short as possible for installation of marine scrubbers on existing and new vessels. Rapid and reliable service is increasingly gaining importance. Furthermore, long maintenance intervals, reliability and durability of the scrubbers as well as a maintenance-friendly design bring benefits to your customers. In order to meet your needs precisely, flexibly and punctually, we operate Service Centers that offer a...
Open the catalog to page 15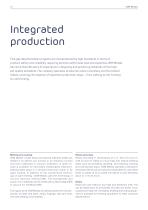
Integrated production Flue gas desulfurization projects are characterized by high standards in terms of product safety and reliability, requiring partners with know-how and expertise. VDM Metals has more than 80 years of experience in designing and producing materials of the highest quality standards. The company operates production sites in Germany and the United S tates, covering the majority of important production steps – from melting to hot forming to cold forming. Melting and casting VDM Metals’ nickel alloys and special stainless steels are melted in an electric arc furnace or an...
Open the catalog to page 16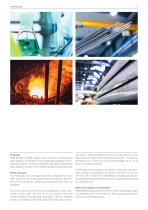
Forgings VDM Metals’ 45 MN forging press uses two anipuators m l and receives its feedstock from dedicated heating and reheating furnaces. Following precisely specified procedures, bars, illets and other semi-finished products are produced. b Rods and bars For the production of forged bars with a diameter of more than 120 mm (4.72 in) and semi-finished products, state-ofthe-art turning lathes, peeling and grinding machines are available. The production of hot-rolled and forged bars with a diameter of less than 120 mm (4.72 in) is performed with modern peeling and grinding machines. A 60-ton...
Open the catalog to page 17All VDM METALS GMBH catalogs and technical brochures
-
Powder
12 Pages
-
Chemical Process Industry
32 Pages
-
Flue Gas Desulfu– rization
28 Pages
-
The world of VDM Metals
5 Pages
-
VDM® Powder 718
5 Pages
-
VDM® Alloy 36
13 Pages
-
VDM® Powder X
5 Pages
-
VDM® Alloy X-750
16 Pages
-
VDM® Alloy 75
7 Pages
-
VDM® Alloy 188
8 Pages
-
VDM® Powder 780
5 Pages
-
VDM Metals Materials Catalog
28 Pages
-
VDM® Alloy 718
13 Pages