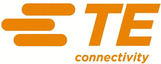

Catalog excerpts
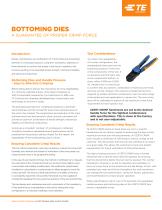
BOTTOMING DIESA GUARANTEE OF PROPER CRIMP FORCE Introduction Design, maintenance, and certification of crimp tooling are all essential elements in crimping production. Long-term consistency depends on these elements to confirm that proper crimp force is applied to the terminal, resulting in the specified tensile strength, mechanical stability, and electrical conductivity. Bottoming Dies and Handle Pressure - Keys to effective Crimping Before being able to discuss the importance of crimp repeatability, it is critical to understand basic crimp theory. Engineers at AMP Incorporated (acquired by Tyco Electronics in 1999, now TE Connectivity) originally developed basic crimp theory and technology as we know it today. The principal parameters for crimping are based on a terminal's stock thickness and the Circular Mil Area (cross sectional area) of the wire to be crimped. The compression and reduction of the cross sectional area (wire and terminal), when correctly calculated, will provide an optimum combination of tensile strength, mechanical stability, and electrical conductivity. As long as a consistent "window” of compression is attained, a similarly consistent, repeatable level of performance can be predicted for the products being crimped. For this reason, the repeatability of the tooling being used is critical. Ensuring Consistent Crimp Results The first critical component in ensuring consistency involves the crimp itself. Generally, two methods are utilized for verification of the crimp areas—by measuring the crimp or by gauging the tooling. In the case of open barrel terminals, the method of verification is to measure the wire barrel of the crimped terminals (i.e., terminal crimp height), using a micrometer with suitably modified jaws. The method for closed barrel (insulated or uninsulated) or coaxial products utilizes gauges to check the crimp tool itself. The second critical requirement is the ability of the tool to consistently repeat the crimp profile. Hand tools must be capable of consistently repeating the cross sectional reduction of the wire and terminal. The tool design and maintenance are both components of this consistency. Crimp performance is standardized in the tool by relating the crimp configuration to a fixed point (setting) of tool operation. Tool Considerations To confirm the repeatability of a crimp configuration, the standardized fixed point are the bottoming surfaces of the wire crimp components of the tool. It is necessary that the tool's wire crimp components bottom, or close, within 0.025 mm [0.001 in]. Handle force is a key factor to confirm that any specific combination of hand tool, terminal, and wire can be crimped. This requires considering the force required to achieve optimum compression over the entire range of terminals and wire applicable to a given tool. The wire crimp jaws will be calibrated to bottom at the maximum crimp force requirement for each specific tool. CERTI-CRIMP hand tools are set to the desired handle force for the tightest conformance with specifications. This is done at the factory and is not user-adjustable. Ensuring Consistent Crimp Results TE CERTI-CRIMP premium hand tools are set to a specific handle force at our factory, based on bottoming the dies at their maximum terminal and wire requirements. All CERTI-CRIMP tools include a Certificate of Certification without charge to the customer. This documents that the tool was certified at our plant on a given date. This allows the customer to track and predict requirements for future verification of tool performance. The high crimping precision of CERTI-CRIMP tools is further enhanced with a ratchet which aids the operator by ensuring that the die bottoms before the tool can be opened. This ratchet mechanism, however, is an aid to operation and subsidiary in terms of crimp force to the actual tool and die design. In fact, with extended use, wear and friction throughout the tool mechanism can change the tool performance, calling for factory adjustment and recertification to ensure proper operation. When specifications call for use of TE terminals, the repeatable handle pressure and bottoming dies of the CERTI-CRIMP tool ensure a repeatable crimp. APPLICATION TOOLING /// BOTTOMING DIES WHITE PAPER
Open the catalog to page 1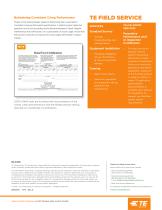
SERVICES Standard Service • Includes troubleshooting and making repairs Equipment Installation • Providing installation, set-up and training at time of equipment delivery Training • Basic Crimp Theory • Hand tool, applicator and equipment set-up, operation and maintenance Maintaining Consistent Crimp Performance Proper crimp tooling design, based on bottoming dies, is essential to consistent crimping that meets specifications. A ratchet system helps the operator use the tool according to the terminal designer's intent. Regular maintenance and certification, on a cycle based on actual usage,...
Open the catalog to page 2All TE CONNECTIVITY LTD. catalogs and technical brochures
-
CeeLok FAS-T Connectors
12 Pages
-
Splash proof micro-USB Connector
10 Pages
-
MODEL 3038 ACCELEROMETER
3 Pages
-
MODEL 3801A
4 Pages
Archived catalogs
-
CRIMPING TERMINALS
8 Pages
-
CEELOK FAS-T* Cable Harness
6 Pages
-
MODEL 3255A ACCELEROMETER
3 Pages
-
MODEL 3803A
4 Pages