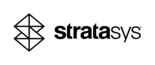

Catalog excerpts
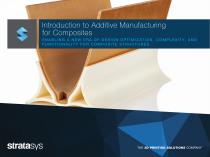
Introduction to Additive Manufacturing for Composites E N A B L I N G A N E W E R A O F D E S I G N O P T I M I Z AT I O N , C O M P L E X I T Y, A N D FUNCTIONALITY FOR COMPOSITE STRUCTURES
Open the catalog to page 1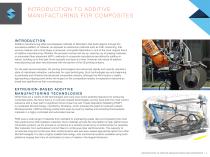
INTRODUCTION Additive manufacturing (AM) encompasses methods of fabrication that build objects through the successive addition of material, as opposed to subtractive methods such as CNC machining, that remove material until a final shape is achieved. Composite fabrication is one of the most original forms of additive manufacturing. Whether the process involves wet lay-up, hand lay-up of prepreg materials, or automated fiber placement (AFP), methods of composite manufacture are distinctly additive in nature, building up to final part forms typically one layer at a time. However, the nature...
Open the catalog to page 2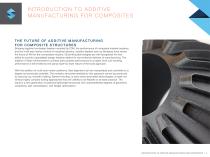
T H E F U T U R E O F A D D I T I V E M A N U FA C T U R I N G FOR COMPOSITE STRUCTURES Bringing together the design freedom enabled by FDM, the performance of composite material systems, and the multi-axis motion control of industrial robotics, industry leaders such as Stratasys have shown the future of AM for the composites industry. 3D printing technologies are well recognized for their ability to provide unparalleled design freedom relative to conventional methods of manufacturing. The addition of fiber reinforcement to printed parts pushed performance to a higher level, but resulting...
Open the catalog to page 3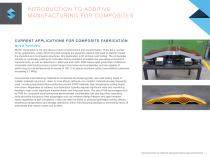
C U R R E N T A P P L I C AT I O N S F O R C O M P O S I T E FA B R I C AT I O N MOLD TOOLING AM for composites is not only about a future of prominence and transformation. There are a number of key applications where 3D printing technologies are presently relevant and used to directly impact the manufacture of composite structures. One application is 3D printed mold tooling. The composites industry is continually pushing for innovative tooling solutions to enable new use cases and product improvements, as well as reductions in lead time and costs. FDM allows rapid production of effective...
Open the catalog to page 4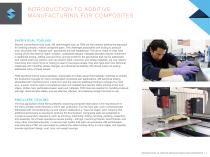
SACRIFICIAL TOOLING Beyond conventional mold tools, AM technologies such as FDM are also directly altering the approach for creating complex, hollow composite parts. The challenges associated with tooling to produce such structures with “trapped tool” geometries are well established. The use of metal or other hard tooling drives the need for highly complex, collapsible designs. Inflatable bladders require investment in additional tooling, adding cost and time, and are limited in the geometries that can be addressed. And typical wash-out options, such as eutectic salts, ceramics, and similar...
Open the catalog to page 5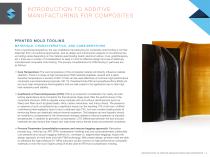
PRINTED MOLD TOOLING M AT E R I A L S , C H A R A C T E R I S T I C S , A N D C O N S I D E R AT I O N S From a functional perspective, the use of additive manufacturing for composite mold tooling is not that dissimilar from conventional approaches. Just as design and construction aspects of conventional layup tooling varies depending on the material used (tooling board, aluminum alloys, Invar, graphite/epoxy, etc.), there are a number of considerations to keep in mind for effective design and use of additively manufactured composite mold tooling. The primary considerations for FDM tooling...
Open the catalog to page 6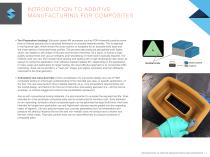
• Tool Preparation (sealing): Extrusion-based AM processes such as FDM inherently produce some level of internal porosity due to physical limitations of extruded material profiles. This is depicted in the figure at right, which shows the cross-section of toolpaths for an example build layer and the cross-section of extruded bead profiles. The process also produces perceptible build layers, which vary based on the shape of the part and the layer thickness. As a result, to ensure a highquality surface finish and vacuum integrity, post-processing of mold tools is typically required. The method...
Open the catalog to page 7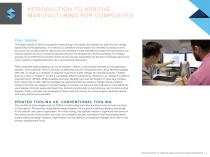
TOOL DESIGN One major benefit of AM for composite mold tooling is the ability and freedom to tailor the tool design specifically to the application. For instance, a schedule-critical repair tool intended to produce one to two parts can be optimized for rapid build time whereas a mold intended for longer-term production use requires greater scrutiny in nearly all aspects and can be designed and built accordingly. The design process for an FDM tool is primarily driven by the process parameters for the final composite parts (cure cycle, pressure, bagging approach, etc.), as previously...
Open the catalog to page 8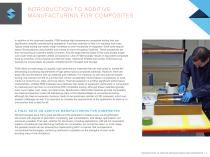
In addition to the business benefits, FDM enables high-temperature composite tooling that can significantly simplify manufacturing operations. A primary example of this is in resulting tool mass. Typical metal tooling can easily weigh hundreds or even thousands of kilograms. Such tools require heavy-lift procedures using forklifts and cranes to move throughout facilities. These procedures are time-consuming and present safety concerns. And the large thermal mass of the tools dictate longer cure cycle times and greater utilities consumption. Use of FDM typically results in equivalent...
Open the catalog to page 9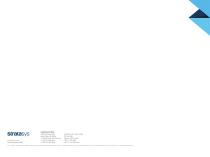
stratasys STRATASYS.COM ISO 9001:2008 Certified © 2017 Stratasys. All rights reserved. Stratasys, Stratasys signet and FDM are trademarks of Stratasys Ltd. and/or its subsidiaries or affiliates and may be registered in certain jurisdictions. All other trademarks belong to their respective owners. eB_FDM_IntroToAM_0317a
Open the catalog to page 10All STRATASYS GMBH catalogs and technical brochures
-
OBJET30
2 Pages
-
Objet1000 Plus
2 Pages
-
The Stratasys F123 Series
4 Pages
-
Fortus® 380/450mc
21 Pages
-
uPrint® SE/uPrint® SE Plus
12 Pages
-
J750 spec sheet
4 Pages
-
Fortus 900mc spec sheet
2 Pages