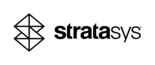

Catalog excerpts
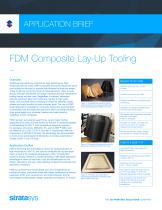
APPLICATION BRIEF FDM Composite Lay-Up Tooling Overview Traditional manufacturing methods for high-performance, fiberreinforced polymer matrix (FRP) composite structures require the use of hard tooling for the mold or mandrel that dictates the final part shape. These molds are commonly made of metal (aluminum, steel, or Invar alloys), although specialized composite materials and high temperature tooling boards are also used. Regardless of material, fabrication requires significant labor and machining, leading to high costs, waste, and long lead times consisting of weeks for relatively simple shapes and many months for more complex tools. The use of FDM® (fused deposition modeling) for composite tooling has demonstrated considerable cost and lead time reductions while providing numerous other advantages such as design freedom and rapid iteration, regardless of part complexity. BENEFITS OF FDM Reduces lead time from months to days. Lowers tooling costs by >50%. Figure 1: Composite aerodynamic fairing (right) produced on a lay-up tool (left) made from high-temperature ULTEM 1010 resin. Simplifies tool design and fabrication with increased functionality. Withstands high temperature autoclave and oven cure cycles (>350 °F, 100 psig). FDM has been successfully used for lay-up and repair tooling applications for years, but was limited by the lack of materials capable of withstanding the 350 °F cure temperature frequently required for aerospace structures. ABS/ASA, PC, and ULTEM™ 9085 resin are effective up to 180 °F, 270 °F, and 300 °F, respectively. With the introduction of ULTEM 1010 resin, the technology has demonstrated numerous new advantages for fabrication at process parameters in excess of 350 °F and 100 psig. Application Outline Enables cost-effective composite part prototyping. Provides low-hassle, sacrificial and wash-out solutions for complex, trapped-tooling applications. Permits trouble-free design changes and iteration to modify tool designs. Figure 2: Composite laminate produced on a lay-up tool made from ULTEM 1010 resin. FDM is becoming the technology of choice for rapid production of high temperature (>350 °F), low volume composite lay-up and repair tools, as well as for moderate temperature (<350 °F) production sacrificial tooling. Relative to traditional tooling, FDM offers significant advantages in terms of lead time, cost, and simplification of tool design, fabrication and use, while enabling increased functionality and geometric complexity. Lay-up and repair tools required in days, not months. FDM lay-up tools have similar design and use considerations as traditional tooling, particularly those with higher coefficients of thermal expansion (CTE), such as aluminum and tooling boards, but the technology provides greater design capability and freedom. To ensure Tool sizes fit within the build volume of the Fortus 900mc™ 3D Printer, although segmented tools are feasible. Moderate cure temperature sacrificial tooling (<350 °F). Relatively low part volumes (10s – 100s vs. 1000s). Figure 3: “Pan skin” lay-up tool (for a commercial aircraft thrust reverser) made from ULTEM 1010 resin. Tool geometries that benefit from higher CTE materials (e.g. male mandrels for increased part compaction).
Open the catalog to page 1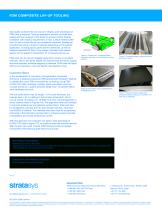
FDM COMPOSITE LAY-UP TOOLING high quality surface finish and vacuum integrity, post-processing of FDM tools is required. Tools are abraded to smooth out build lines, sealed and then undergo a final polish to achieve surface finishes consistent with industry requirements. In fact, surface finishes better than 16 micro-inches Ra can be consistently achieved. Sealing can be performed using a range of materials depending on the specific application, including epoxy paste and film adhesives, as well as adhesive-backed FEP films. Once sealed, standard mold release agents can be applied in...
Open the catalog to page 2All STRATASYS GMBH catalogs and technical brochures
-
OBJET30
2 Pages
-
Objet1000 Plus
2 Pages
-
The Stratasys F123 Series
4 Pages
-
Fortus® 380/450mc
21 Pages
-
uPrint® SE/uPrint® SE Plus
12 Pages
-
J750 spec sheet
4 Pages
-
Fortus 900mc spec sheet
2 Pages