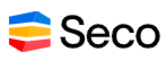
Catalog excerpts
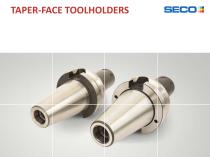
TAPER-FACE TOOLHOLDERS
Open the catalog to page 1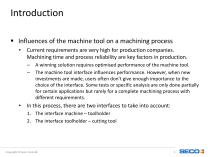
Introduction Influences of the machine tool on a machining process • Current requirements are very high for production companies. Machining time and process reliability are key factors in production. – – A winning solution requires optimised performance of the machine tool. The machine tool interface influences performance. However, when new investments are made, users often don’t give enough importance to the choice of the interface. Some tests or specific analysis are only done partially for certain applications but rarely for a complete machining process with different requirements. In...
Open the catalog to page 2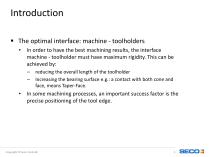
Introduction The optimal interface: machine - toolholders • In order to have the best machining results, the interface machine - toolholder must have maximum rigidity. This can be achieved by: – – reducing the overall length of the toolholder Increasing the bearing surface e.g.: a contact with both cone and face, means Taper-Face. In some machining processes, an important success factor is the precise positioning of the tool edge.
Open the catalog to page 3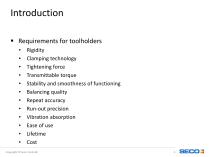
Introduction Requirements for toolholders • • • • • • • • • • • • Rigidity Clamping technology Tightening force Transmittable torque Stability and smoothness of functioning Balancing quality Repeat accuracy Run-out precision Vibration absorption Ease of use Lifetime Cost
Open the catalog to page 4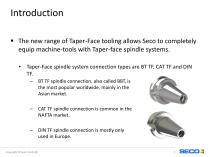
Introduction The new range of Taper-Face tooling allows Seco to completely equip machine-tools with Taper-face spindle systems. • Taper-Face spindle system connection types are BT TF, CAT TF and DIN TF. – BT TF spindle connection, also called BBT, is the most popular worldwide, mainly in the Asian market. CAT TF spindle connection is common in the NAFTA market. DIN TF spindle connection is mostly only used in Europe.
Open the catalog to page 5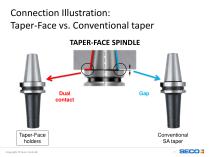
Connection Illustration: Taper-Face vs. Conventional taper TAPER-FACE SPINDLE Dual contact Taper-Face holders Copyright © Seco Tools AB
Open the catalog to page 7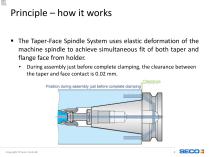
Principle – how it works The Taper-Face Spindle System uses elastic deformation of the machine spindle to achieve simultaneous fit of both taper and flange face from holder. • During assembly just before complete clamping, the clearance between the taper and face contact is 0.02 mm. Copyright © Seco Tools A
Open the catalog to page 8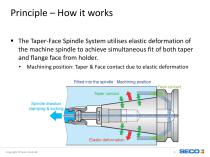
Principle – How it works The Taper-Face Spindle System utilises elastic deformation of the machine spindle to achieve simultaneous fit of both taper and flange face from holder. • Machining position: Taper & Face contact due to elastic deformation Copyright © Seco Tools A
Open the catalog to page 9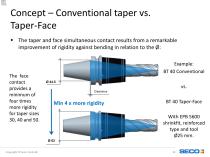
Concept – Conventional taper vs. Taper-Face The taper and face simultaneous contact results from a remarkable improvement of rigidity against bending in relation to the Ø: The face contact provides a minimum of four times more rigidity for taper sizes 30, 40 and 50. BT 40 Taper-Face With EPB 5600 shrinkfit, reinforced type and tool Ø25 mm. Copyright © Seco Tools
Open the catalog to page 10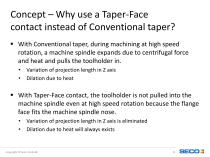
Concept – Why use a Taper-Face contact instead of Conventional taper? With Conventional taper, during machining at high speed rotation, a machine spindle expands due to centrifugal force and heat and pulls the toolholder in. • • Variation of projection length in Z axis Dilation due to heat With Taper-Face contact, the toolholder is not pulled into the machine spindle even at high speed rotation because the flange face fits the machine spindle nose. • • Variation of projection length in Z axis is eliminated Dilation due to heat will always exists
Open the catalog to page 11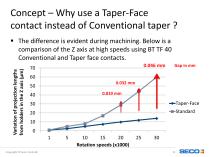
Concept – Why use a Taper-Face contact instead of Conventional taper ? Variation of projection lengths from holders in the Z axis (µm) The difference is evident during machining. Below is a comparison of the Z axis at high speeds using BT TF 40 Conventional and Taper face contacts. 0.046 mm Copyright © Seco Tools AB
Open the catalog to page 12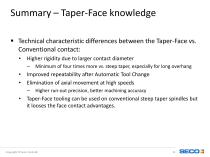
Summary – Taper-Face knowledge Technical characteristic differences between the Taper-Face vs. Conventional contact: • Higher rigidity due to larger contact diameter – Improved repeatability after Automatic Tool Change Elimination of axial movement at high speeds – Minimum of four times more vs. steep taper, especially for long overhang Higher run-out precision, better machining accuracy Taper-Face tooling can be used on conventional steep taper spindles but it looses the face contact advantages.
Open the catalog to page 13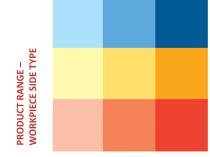
PRODUCT RANGE – WORKPIECE SIDE TYPE
Open the catalog to page 14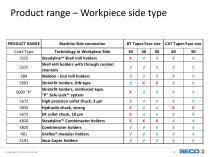
Product range – Workpiece side type PRODUCT RANGE Machine Side connection Code Type Technology at Workpiece Side Steadyline™ Shell mill holders Shell mill holders with through coolant channels Weldon - End mill holders Shrinkfit holders, DIN type Shrinkfit holders, reinforced type. "P" Safe-Lock™ system High precision collet chuck, 3 µm Hydraulic chuck, strong ER collet chuck, 10 µm Steadyline™ Combimaster holders Combimaster holders Graflex® modular holders Seco-Capto holders
Open the catalog to page 15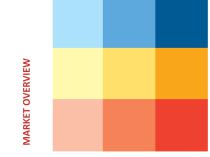
MARKET OVERVIEW
Open the catalog to page 16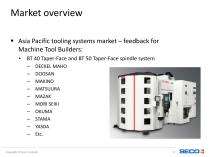
Market overview Asia Pacific tooling systems market – feedback for Machine Tool Builders: • BT 40 Taper-Face and BT 50 Taper-Face spindle system – – – – – – – – – – DECKEL MAHO DOOSAN MAKINO MATSUURA MAZAK MORI SEIKI OKUMA STAMA YASDA Etc.
Open the catalog to page 17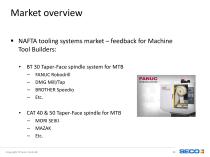
Market overview NAFTA tooling systems market – feedback for Machine Tool Builders: • BT 30 Taper-Face spindle system for MTB – – – – FANUC Robodrill DMG Mill/Tap BROTHER Speedio Etc. MORI SEIKI MAZAK Etc.
Open the catalog to page 18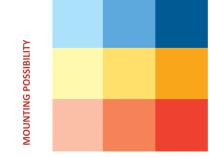
MOUNTING POSSIBILITY
Open the catalog to page 19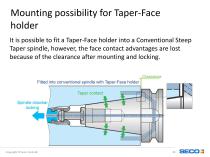
Mounting possibility for Taper-Face holder It is possible to fit a Taper-Face holder into a Conventional Steep Taper spindle, however, the face contact advantages are lost because of the clearance after mounting and locking. Copyright © Seco Tools AB
Open the catalog to page 20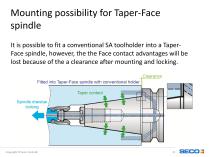
Mounting possibility for Taper-Face spindle It is possible to fit a conventional SA toolholder into a TaperFace spindle, however, the the Face contact advantages will be lost because of the a clearance after mounting and locking. Copyright © Seco Tools AB
Open the catalog to page 21All SECO TOOLS catalogs and technical brochures
-
Solid End Mills.pdf
641 Pages
-
Indexable Milling Catalog.pdf
856 Pages
-
GL25-HEADS RANGE EXPANSION
13 Pages
-
SECO NEWS SUMMARY 2019.1
9 Pages
-
DOUBLE OCTOMILL™
2 Pages
-
PRODUCT SUMMARY
2 Pages
-
SECO NEWS SUMMARY 2018.1
14 Pages
-
POZVÁNKA ZD KOVOSVIT
1 Pages
-
Machinability_poster
1 Pages
-
SQUARE T4
2 Pages
-
SECO Product summary
2 Pages
-
SECO NEWS
310 Pages
-
DURATOMICTM
16 Pages
-
QUATTROMILL-AL™
2 Pages
Archived catalogs
-
DISC MILLING
36 Pages