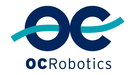
Catalog excerpts
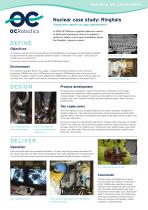
Nuclear case study: Ringhals Snake-arm robots for pipe replacement In 2005 OC Robotics supplied snake-arm robots to Uddcomb Engineering (Areva) to replace a section of safety critical pipe immediately below the Ringhals 1 pressure vessel. DEFINE Objectives To replace a section of a thick wall stainless steel SCRAM pipe by providing remote handling capability to operate within a highly inaccessible network of pipes – nicknamed ’The Jungle’ – using only preexisting access routes (Fig 1). To provide a generic method to access all 157 SCRAM pipe nozzles. Environment The Common Insulation Room, ’the Jungle’, contains 157, 205mm diameter control rod drive mechanism (CRDM) tubes. Each CRDM tube has a dedicated SCRAM pipe which forms part of the emergency shutdown system. Access between the CRDM tubes is via 80mm wide corridors which are up to 6m long. The Jungle is accessed via a temporary ladder and peripheral crawl-space (Fig 2). Process development The project was completed in under 9 months from notification of the urgent requirement to completion of site acceptance tests and trial deployment. This included design of two snake-arm systems and development of a multi-stage process involving four tools. Partners included Uddcomb Engineering and Climax Precision Machine Tools. Two snake-arms The first snake-arm was a compliant 800mm long, 40mm diameter, 23 degree-offreedom snake-arm. The snake-arm entered the Jungle through pre-existing 60mm diameter holes in the floor and snaked around obstructing pipes to gain the ideal view of the work site (Fig 3). Fig 3. Gaining an ideal view of the worksite Fig 4. The congested work site showing both snake-arms The second snake-arm was 600mm long, 60mm diameter, with 13 degrees-of-freedom (Fig 4). This snake-arm used a wrist and gripper to deliver: fixtures and jigs to secure the pipe; cutters for the ‘inside-to-out’ cutting tool; a tack welding head; a gas shield and an x-ray film holder. Point to point, computer controlled motion resolution was better than 20 microns. DELIVER Operation The actual pipe repair was completed manually in 3 days, using the processes developed for the robots, as it was just within reach. Subsequently the robots replicated the manual process in less than 24 hours with no manual intervention and demonstrated the generic solution. Fig 7. Replaced section of pipe Fig 6. Nozzle reshaping prior to inserting the new section of pipe The pipe repair at Ringhals was a world first. The snake-arm solution showed that all 157 SCRAM pipes could be accessed using the same equipment and procedures. This successful demonstration was a key requirement of the safety case, allowing the plant to come back online. The snake-arms delivered and positioned a wide range of tools with precision and flexibility, within hazardous, con
Open the catalog to page 1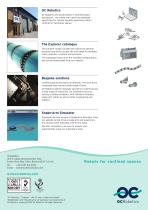
OC Robotics OC Robotics are world leaders in confined space automation - our snake-arm robots are designed specifically for remote handling operations within confined or hazardous spaces. The Explorer catalogue The Explorer range of snake-arm robots are general purpose tools which occupy the mid-range for diameter, reach, payload, curvature and precision. The catalogue shows all of the available configurations and can be downloaded from our website. Bespoke solutions Confined spaces are nearly all different. The work to be completed may involve a wide range of tools. OC Robotics delivers...
Open the catalog to page 2All OC Robotics catalogs and technical brochures
-
Series II - X125
2 Pages
-
LaserPipe Case Study
1 Pages
-
LaserSnake2
2 Pages
-
Series II, X125 System
2 Pages