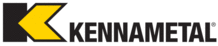

Catalog excerpts
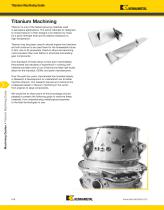
Titanium Machining Titanium is one of the fastest growing materials used in aerospace applications. The prime rationale for designers to chose titanium in their designs is its relative low mass for a given strength level and its relative resistance to high temperature. Titanium has long been used in aircraft engine front sections and will continue to be used there for the foreseeable future. In fact, due to its properties, titanium alloys are becoming more prevalent than ever before in structural and landing gear components. One drawback of these alloys is their poor machinability. Kennametal has decades of experience in working with material providers (one of our divisions provides high-purity alloys for the industry), OEMs, and parts manufacturers. Over the past few years, Kennametal has invested heavily in Research & Development to understand how to better machine titanium. Our research has led us to become the undisputed leader in titanium machining in the world, from engines to large components. We would like to share some of this knowledge and are pleased to present the following guide to machine these materials, from understanding metallurgical properties to the best technologies to use. Machining Guides • Titanium Machining Guide KENNAMETAL www.kennametal.com
Open the catalog to page 1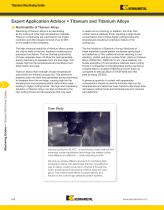
Titanium Machining Guide Expert Application Advisor • Titanium and Titanium Alloys Machinability of Titanium Alloys Machining of titanium alloys is as demanding as the cutting of other high-temperature materials. Titanium components are machined in the forged condition and often require removal of up to 90% of the weight of the workpiece. to depth-of-cut notching. In addition, the Chip-Tool contact area is relatively small, resulting in large stress concentration due to these higher cutting forces and temperatures resulting in premature failure of the cutting tool. The high-chemical...
Open the catalog to page 3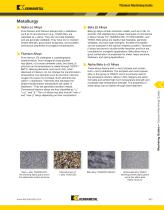
Titanium Machining Guide Metallurgy Alpha (α) Alloys Pure titanium and titanium alloyed with α stabilizers, such as tin and aluminum (e.g., Ti5Al2.5Sn), are classified as α alloys. They are non-heat treatable and are generally weldable. They have low to medium tensile strength, good notch toughness, and excellent mechanical properties at cryogenic temperatures. Beta (β) alloys contain transition metals, such as V, Nb, Ta, and Mo, that stabilize the β phase. Examples of commercial β alloys include Ti11.5Mo6Zr4.5Sn, Ti15V3Cr3Al3Sn, and Ti5553. Beta alloys are readily heat-treatable, generally...
Open the catalog to page 4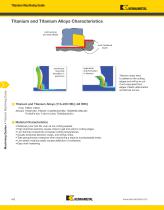
Titanium Machining Guide Titanium and Titanium Alloys Characteristics cold workini and heat effe< work-hardened layers continuous long chip Machining Guides • Titanium Machining Guide ^Titanium and Titanium Alloys (110-450 HB) (<48 HRC) Pure: Ti98.8, Ti99.9 Alloyed: Ti5Al2.5Sn, Ti6Al4V, Ti4Al2Sn4Zr2Mo, Ti3Al8V6Cr4Mo4Zr, Ti10V2Fe 3Al, Ti13V11Cr3Al, Ti5Al5Mo5V3Cr ^ Material Characteristics • Relatively poor tool life, even at low cutting speeds. • High chemical reactivity causes chips to gall and weld to cutting edges. • Low thermal conductivity increases cutting temperatures. • Usually...
Open the catalog to page 5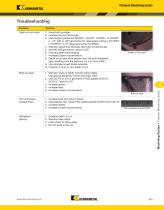
Titanium Machining Guide Troubleshooting Depth-of-cut notch Built-up edge Solution 1. Avoid built-up edge. 2. Increase the tool lead angle. 3. Use tougher grades like KC5525™, KCU25™, KCM25™, or KCM35™ in -UP, -MP, or -RP geometries for interrupted cutting or KC725M™ or KCPK30™ in “S” edge geometries for Milling. 4. Maintain speed and decrease feed rate simultaneously. 5. Use MG-MS geometry in place of GP. 6. Ensure proper insert seating. 7. Increase coolant concentration. 8. Depth of cut should be greater than the work-hardened layer resulting from the previous cut (>0,12mm/.005"). 9. Use...
Open the catalog to page 6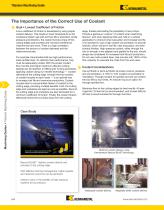
Titanium Machining Guide The Importance of the Correct Use of Coolant Goal • Lowest Coefficient of Friction A low coefficient of friction is developed by using proper coolant delivery. This results in lower temperature so the workpiece doesn’t get soft and tool life is extended. Under pressure and direction, the coolant knocks chips off the cutting edges and provides anti-corrosive benefits for machine tool and work. There is a high correlation between the amount of coolant delivered and the metal removal rate. Machining Guides • Titanium Machining Guide For example, Kennametal drills are...
Open the catalog to page 7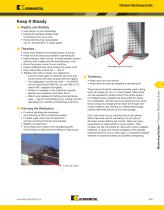
Titanium Machining Guide Keep It Steady ^ Rigidity and Stability • Use gravity to your advantage. • Horizontal spindles enable chips to fall away from your work. • Horizontal fixturing necessitates use of “tombstones” or angle plates. ^ Therefore... • Keep work closest to strongest points of fixture. • Keep work as close as possible to spindle/quill. • High-pressure, high-volume, through-spindle coolant delivery will increase tool life tremendously (>4x). • Know the power curve of your machine. • Ensure sufficient axis drive motors for power cuts. • Every setup has a weak link — find it! •...
Open the catalog to page 8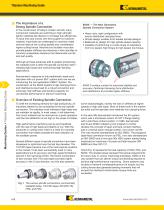
Titanium Machining Guide The Importance of a Strong Spindle Connection In the construction of today’s modern aircraft, many component materials are switching to high-strength lighter materials like titanium to increase fuel efficiencies. To save time and money with this tougher-to-machinematerial, machinists are challenged to maximize metal removal rates at low cutting speeds and considerably higher cutting forces. Machine tool builders must also provide greater stiffness and damping in their spindles to minimize undesirable vibrations that deteriorate tool life and part quality. KM4X — The...
Open the catalog to page 9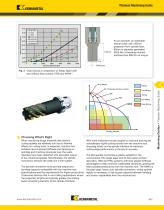
Titanium Machining Guide As an example, an indexable helical cutter with 250mm projection from spindle face, 80mm in diameter generates 4620 Nm of bending moment and less than 900 Nm of torque. Fig. 2 Chart shows a comparison of Steep Taper with and without face contact, HSK and KM4X ™. Face Milling Turning PSC End Milling Deep Boring Bending Moment Choosing What’s Right When machining tough materials like titanium, cutting speeds are relatively low due to thermal effects on cutting tools. In response, machine tool builders have improved stiffness and damping on spindles and machine...
Open the catalog to page 10All KENNAMETAL FRANCE catalogs and technical brochures
-
KenCast™
20 Pages
-
Master Catalog 2018
1 Pages
-
MASTER CATALOG
1 Pages
-
INNOVATIONS 2019
1 Pages
-
Tooling Systems News
3 Pages
-
Snowplow Blades
1 Pages
-
Road Rehabilitation Road King
24 Pages
-
export unsecure
164 Pages
-
High-Temperature Machining
16 Pages
-
Composite Machining
22 Pages
-
Solutions for Aerospace
684 Pages