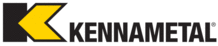

Catalog excerpts
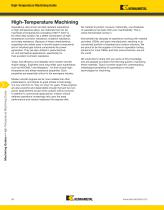
High-Temperature Machining Guide Superalloys, also known as heat-resistant superalloys or high-temperature alloys, are materials that can be machined at temperatures exceeding 1000° F (540° C). No other alloy system has a better combination of high-temperature corrosion resistance, oxidation resistance, and creep resistance. Because of these characteristics, superalloys are widely used in aircraft engine components and in industrial gas turbine components for power generation. They are also utilized in petrochemical, oil, and biomedical applications, specifically for their excellent corrosion resistance. Today, fuel efficiency and reliability drive modern aircraft engine design. Engineers have long relied upon superalloys, such as INCONEL® and Waspaloy™, for their unique high-temperature and stress-resistance properties. Such properties are especially critical to the aerospace industry. No material is perfect, however. Historically, one drawback of superalloys has been their poor machinability. This is where Kennametal comes in. Kennametal has decades of experience working with material providers, OEMs, and parts manufacturers, resulting in an unmatched portfolio of standard and custom solutions. We are proud to be the supplier of choice in superalloy tooling solutions for most OEMs, and their subcontractors, around the world. We would like to share with you some of this knowledge, and are pleased to present the following guide to machining these materials. Topics covered range from understanding metallurgical properties of superalloys to the best technologies for machining. Machining Guides • High-Temperature Machining Guide Modern aircraft engines are far more reliable than their predecessors, and thanks to great strides in technology, it is now common to “stay on wing” for years. These engines are also powerful and dependable enough that just two can power large jetliners across entire oceans without concern. In addition to commercial applications, mission-critical defense operations increasingly rely upon the peak performance and mission readiness the engines offer. KENNAMETAL www.kennametal.com
Open the catalog to page 1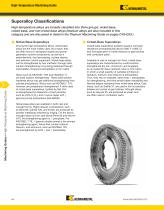
High-Temperature Machining Guide Superalloy Classifications High-temperature alloys are broadly classified into three groups: nickel-base, cobalt-base, and iron-nickel-base alloys (titanium alloys are also included in this category and are discussed in detail in the Titanium Machining Guide on pages D18–D33.) Nickel-Base Superalloys Cobalt-Base Superalloys Among the high-temperature alloys, nickel-base alloys are the most widely used. As a result, they are often found in aerospace engine and power generation turbine components, as well as in petrochemical, food processing, nuclear reactor,...
Open the catalog to page 3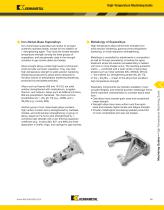
High-Temperature Machining Guide^ Iron-Nickel-Base Superalloys ^ Iron-nickel-base superalloys are similar to wrought austenitic stainless steels, except for the addition of y' strengthening agent. They have the lowest elevated temperature strength among the three groups of superalloys, and are generally used in the wrought condition in gas turbine disks and blades. Most wrought alloys contain high levels of chromium, which provide corrosion resistance. They owe their high-temperature strength to solid solution hardening (hardening produced by solute atoms dissolved in the alloy matrix)...
Open the catalog to page 4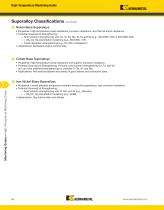
High-Temperature Machining Guide Superalloy Classifications (continued) Nickel-Base Superalloys • Properties: High-temperature creep resistance, corrosion resistance, and thermal shock resistance. • Potential Source(s) of Strengthening: — Solid solution strengthening with Co, Cr, Fe, Mo, W, Ta, and Re (e.g., INCONEL® 600 or INCONEL 625) — γ´ (Ni3 [Al, Ti]) precipitation hardening (e.g., INCONEL 718) — Oxide-dispersion strengthening (e.g., IN-100 or Waspaloy®) • Applications: Aerospace engine components. Cobalt-Base Superalloys • Properties: High-temperature creep resistance and superior...
Open the catalog to page 5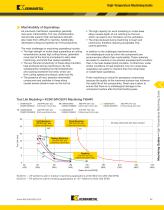
High-Temperature Machining Guide Machinability of Superalloys As previously mentioned, superalloys generally have poor machinability. The very characteristics that provide superior high-temperature strength also make them difficult to machine. Additionally, decreased cutting tool speeds can limit productivity. • The high capacity for work hardening in nickel-base alloys causes depth-of-cut notching on the tool, which can lead to burr formation on the workpiece. • The chip produced during machining is tough and continuous, therefore requiring acceptable chip control geometry. In addition to...
Open the catalog to page 6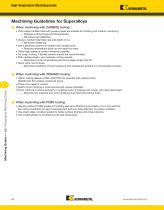
Machining Guidelines for Superalloys ^ When machining with CARBIDE tooling: • PVD coated carbide tools with positive rakes are suitable for finishing and medium machining. — Reduces cutting forces and temperatures — Minimizes part deflection • Always maintain high feed-rate and depth of cut. — Minimizes hardening • Use a generous quantity of coolant with carbide tools. — Reduces temperature build-up and rapid tool wear • Utilize high-pressure coolant whenever possible. • For rough cutting, T-landed ceramic inserts are recommended. • With carbide inserts, use moderate cutting speeds. —...
Open the catalog to page 7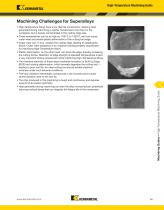
High-Temperature Machining Guide • High-Temperature Alloys have a low thermal conductivity, meaning heat generated during machining is neither transferred to the chip nor the workpiece, but is heavily concentrated in the cutting edge area. • These temperatures can be as high as 1100°C to 1300°C, and can cause crater wear and severe plastic deformation of the cutting tool edge. • Crater wear can, in turn, weaken the cutting edge, leading to catastrophic failure. Crater wear resistance is an important tooling property requirement for machining High-Temperature Alloys. • Plastic deformation,...
Open the catalog to page 8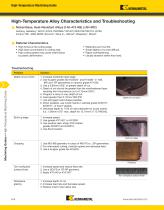
High-Temperature Machining Guide High-Temperature Alloy Characteristics and Troubleshooting Nickel-Base, Heat-Resistant Alloys (140–475 HB) (≤48 HRC) Astroloy, Hastelloy®, B/C/C-276/X, INCONEL® 601/617/625/700/706/718, IN100, Incoloy® 901, MAR-M200, Nimonic®, Rene 41, Udimet®, Waspaloy®, Monel® Material Characteristics • High forces at the cutting edge. • High heat concentration in cutting area. • High cutting speed may cause insert failure by plastic deformation. Relatively poor tool life. Small depths of cut are difficult. Rapid workhardening. Usually abrasive rather than hard....
Open the catalog to page 9All KENNAMETAL FRANCE catalogs and technical brochures
-
KenCast™
20 Pages
-
Master Catalog 2018
1 Pages
-
MASTER CATALOG
1 Pages
-
INNOVATIONS 2019
1 Pages
-
Tooling Systems News
3 Pages
-
Snowplow Blades
1 Pages
-
Road Rehabilitation Road King
24 Pages
-
export unsecure
164 Pages
-
Titanium Machining
16 Pages
-
Composite Machining
22 Pages
-
Solutions for Aerospace
684 Pages