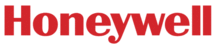

Catalog excerpts
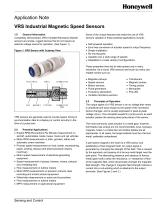
Application Note VRS Industrial Magnetic Speed Sensors 1.0 General Information Completely self-powered, VRS (Variable Reluctance Speed) sensors are simple, rugged devices that do not require an external voltage source for operation. (See Figure 1.) Figure 1: VRS Sensor with Cutaway View Some of the unique features that make the use of VRS sensors valuable in these potential applications include: Self-powered operation Error-free conversion of actuator speed to output frequency Simple installation No moving parts Useable over a wide range of speeds Adaptable to a wide variety of configurations These properties have led to wide-spread use in many industries. As a result, VRS sensors are known by many userelated names such as: Magnetic-pickups Speed sensors Motion sensors, Pulse generators Frequency generators Variable reluctance sensors VRS sensors are generally used to provide speed, timing or synchronization data to a display (or control circuitry) in the form of a pulse train. 2.0 Potential Applications Engine RPM (Revolutions Per Minute) measurement on aircraft, automobiles, boats, buses, trucks and rail vehicles Motor RPM measurement on drills, grinders, lathes and automatic screw machines Process speed measurement on food, textile, woodworking, paper, printing, tobacco and pharmaceutical industry machinery Motor speed measurement of electrical generating equipment Speed measurement of pumps, blowers, mixers, exhaust and ventilating fans Flow measurement on turbine meters Motor RPM measurement on precision camera, tape recording and motion picture equipment Wheel-slip measurement on autos and locomotives Flow measurement on turbine meters MPH measurement on agricultural equipment Transducers Magnetic probes Timing probes Monopoles Pick-offs 3.0 Principles of Operation The output signal of a VRS sensor is an ac voltage that varies in amplitude and wave shape as the speed of the monitored device changes, and is usually expressed in peak-to-peak voltage (Vp-p). One complete waveform (cycle) occurs as each actuator passes the sensing area (pole piece) of the sensor. The most commonly used actuator is a metal gear; however, bolt heads (cap screws are not recommended), keys, keyways, magnets, holes in a metal disc and turbine blades are all appropriate. In all cases, the target material must be a ferrous metal, preferably unhardened. A permanent magnet is the heart of a VRS sensor and establishes a fixed magnetic field. An output signal is generated by changing the strength of this field. This is caused by the approach and passing of a ferrous metal target near the pole piece. The alternating presence and absence of ferrous metal (gear tooth) varies the reluctance, or “resistance of flow” of the magnetic field, which dynamically changes the magnetic field strength. This change in magnetic field strength induces a current into a coil winding which is attached to the output terminals. (See Figures 2 and 3.
Open the catalog to page 1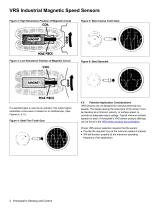
VRS Industrial Magnetic Speed Sensors Figure 2: High Reluctance Position of Magnetic Circuit Figure 5: Steel Coarse Tooth Gear Figure 3: Low Reluctance Position of Magnetic Circuit Figure 6: Steel Sprocket If a standard gear is used as an actuator, this output signal resembles a sine wave if viewed on an oscilloscope. (See Figures 4, 5, 6.) 4.0 Potential Application Considerations VRS sensors are not designed for sensing extremely low speeds. The target passing the pole piece of the sensor must be traveling at a minimum velocity, or surface speed, to provide an adequate output voltage....
Open the catalog to page 2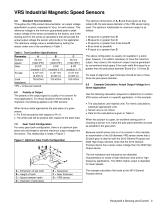
VRS Industrial Magnetic Speed Sensors 5.0 Standard Test Conditions Throughout the VRS product documentation, an output voltage specification is given, expressed in Vp-p, for each sensor. This reference voltage is the minimum guaranteed peak to peak output voltage of the sensor as tested by the factory, and is the starting point for the series of calculations that will provide the actual output voltage the sensor will provide in the application. The reference voltage value is established by testing the sensor under one of the conditions in Table 1. The optimum dimensions of A, B and C are...
Open the catalog to page 3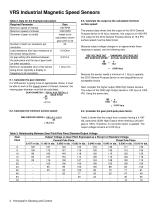
VRS Industrial Magnetic Speed Sensors Table 2. Data for the Example Calculation Required Parameter Minimum speed of interest Maximum speed of interest Diameter of gear (or shaft) Number of teeth (or actuators) per revolution. Load resistance (the input resistance of the sensor being driven). Air gap setting (the distance between the pole piece and the top of gear tooth (or other actuator)). Minimum acceptable Vp-p of the sensor being driven (typically a display or frequency to dc converter). Data 100 RPM 1000 RPM needs to be calculated; known gear pitch is 20 60 8.3. Calculate the output at...
Open the catalog to page 4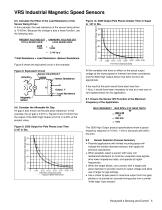
VRS Industrial Magnetic Speed Sensors 8.5. Calculate the Effect of the Load Resistance of the Sensor Being Driven In this example, the load resistance of the sensor being driven is 10 kOhm. Because this change is also a linear function, use the following ratio: Figure 10. 3030 Output Pole Pieces Greater Than or Equal to .187 in Dia. PRESENT VOLTAGE OUT = UNKNOWN VOLTAGE OUT LOAD RESISTANCE TOTAL RESISTANCE* 3.078 11200 *Total Resistance = Load Resistance +Sensor Resistance. Figure 8 shows the equivalent circuit in this example. Figure 8. Equivalent Circuit All the variables that have an...
Open the catalog to page 5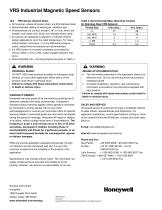
VRS Industrial Magnetic Speed Sensors 10.0 VRS Sensor General Notes All housings, unless otherwise noted, are 303 stainless steel. Recommended cabling is twisted pair, shielded type. All pole pieces are conical, except 0.187 in units, which are straight, and chisel units, which are indicated where used. All sensors are designed to operate in moderate oil/fluid splash applications up to the rated temperature. For heavy oil/fluid splash, immersion. or if any differential pressure exists, sealed front end sensors are recommended. If a VRS sensor is mounted completely surrounded by ferrous...
Open the catalog to page 6All Honeywell | Safety and Productivity Solutions catalogs and technical brochures
-
IH40
2 Pages
-
IH21
2 Pages
-
13 mm series
3 Pages
-
SL-14
3 Pages
-
HG5700
2 Pages
-
HG1930
2 Pages
-
HG1900
2 Pages
-
HG1700
2 Pages
-
HGUIDE N580
4 Pages
-
Test and Measurement
8 Pages
-
MICRO SWITCH™
3 Pages