
Catalog excerpts
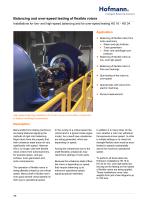
Hofmann. Intelligent Balancing Solutions Balancing and over-speed testing of flexible rotors Installations for low- and high-speed balancing and for over-speed testing HS 16 - HS 34 Application • Balancing of flexible rotors from turbo-machinery • Steam and gas turbines • Turbo generators • Axial- and centrifugal-compressors • Balancing of flexible rotors at low- and high-speed • Balancing of flexible rotors in their own bearings • Spin-testing of the rotors at over-speed • Special tests with rotors from electric machines • Runout-measurement High-speed balancing installation HS 23 with vacuum proof safety containment to balance centrifugal compressors Description Many shafts from rotating machinery are being balanced applying the methods of rigid rotor balancing. Rigid rotors have the property that their unbalance state does not vary significantly with speed. However this is no longer valid with flexible rotors (rotors from turbomachinery, for example steam- and gas turbines, turbo generators and turbo compressors). The operation of flexible rotors is being affected at least by one critical speed. Many (shaft-) flexible rotors even pass several critical speeds on their way to operational speed. In the vicinity of a critical speed the rotors bend in a typical mode (eigenmode). As a result new unbalances are being generated, which are depending on speed. Among the unbalances due to the shaft flexibility unbalances may result from settings of rotor parts. Because the unbalance state of flexible rotors is depending on speed, they require balancing up to maximum operational speed applying special methodes. In addition it is many times of interest, whether a rotor can withstand the exposure at over-speed. In order to initiate settings or to check the strength flexible rotors must be accelerated to speeds substantially above the maximum operational speed. To perform all those tasks the Hofmann installations HS 16 to HS 34 for low- and high-speed balancing and for testing at over-speed of flexible rotors are being applied. Those installations cover rotor weights from just a few kilograms up to 100 tons.
Open the catalog to page 1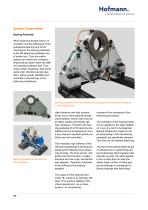
Intelligent Balancing Solutions Bearing pedestal HS 26 with motorized moving gear and automatic clamping on the machine bed System Components Bearing Pedestals When balancing flexible rotors it is important, that the stiftnesses of the operational bearings and of the mounting for the bearing pedestals of the HS balancing installation are of similar size. Then the critical speeds and mainly the corresponding bending modes match the different bearing conditions well. Thus those modal unbalances, that would excite rotor vibrations during operation, will be exactly identified and corrected in...
Open the catalog to page 2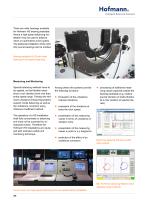
Intelligent Balancing Solutions There are roller bearings available for Hofmann HS bearing pedestals. Hence a high-speed balancing installation may be used to balance rotors on openrollers at low speed. The elaborate installation of the rotor into journal bearings can be omitted. Bearing pedestal HS 28 with roller bearing for low-speed balancing Special balancing methods have to be applied, so that flexible rotors show a low vibration level over their entire speed range. Thereby the Hofmann unbalance measuring systems support modal balancing as well as the unbalance correction using...
Open the catalog to page 3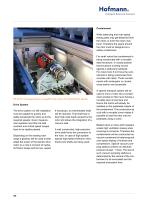
Intelligent Balancing Solutions Drive System The drive system of a HS installation must be capable to quickly and safely accelerate the rotors up to the required speeds. Given measurement speeds must then be held constant and critical speed ranges have to be rapidly passed. Depending on the existing rotor range a gearbox will be used to best adapt the power of the electric drive motor to a rotor's moment of inertia, its friction losses and its max. speed. If necessary, an intermediate shaft will be required. That shaft has to bear high axial loads caused by the rotor and allows the...
Open the catalog to page 4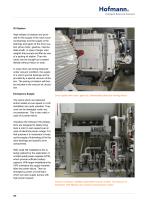
Oil System High-reliable oil stations are provided for the supply of the rotor’s journal bearings and the supply of the bearings and gears of the drive system (drive motor, gearbox, intermediate shaft). In case of larger rotor weights the journals are lifted by use of a jacking oil station. Then the rotors can be brought up to speed literally without friction or wear. In case rotors are being balanced under vacuum condition, the supply of a rotor’s journal bearings will be provided by a special vacuum oil station. The jacking oil station will then be included in the vacuum oil circulation....
Open the catalog to page 5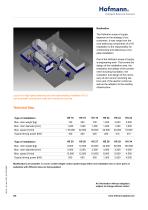
Hofmann. Intelligent Balancing Solutions Realisation The Hofmann scope of supply depends on the strategy of our customers. It may range from the core balancing components of a HS installation to the responsibility for constructing and delivering a complete installation. Part of the Hofmann scope of supply is engineering work. That covers the design of the installation area, the evaluation and design of the containment including foundation, the evaluation and design of the necessary oil and vacuum pumping stations and of the electric control as well as the adaption to the existing...
Open the catalog to page 6