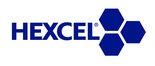

Catalog excerpts
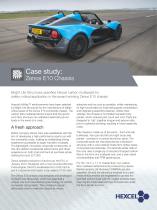
Case study:Zenos E10 ChassisBright Lite Structures specifies Hexcel carbon multiaxials for safety-critical application in the award-winning Zenos E10 chassis Hexcel’s HiMax™ reinforcements have been selected by Bright Lite Structures for the manufacture of safety-critical areas of the Zenos E10 composite chassis. The carbon fibre multiaxial fabrics ensure that the sports car’s floor structure can withstand seat belt pull-out loads in the event of a crash. A fresh approach British company Zenos Cars was established with the aim of developing a high performance sports car with low ownership costs, making an exhilarating driving experience accessible to larger numbers of people. The lightweight, innovative composite construction of the cars delivers exceptional performance and driver experience on both road and track at purchase prices starting from just £27,000. Zenos started production of its first car, the E10, in January 2015. Equipped with a mid-mounted 200 bhp 2-litre engine, the E10 accelerates from 0-60 mph in just 4.5 seconds and boasts a top speed of 135 mph. The Zenos E10 chassis was designed and developed by Bright Lite Structures, which has patented a unique, low cost manufacturing technology for carbon composite components. The company’s design philosophy was to make the chassis as simple, attractive and low cost as possible, whilst maintaining its high functionality by maximising parts consolidation and integrating assembly features. Unlike other vehicles, the chassis is not hidden beneath body panels, which reduces part count and cost. Parts are designed to ‘clip’ together tongue-and-groove style, prior to adhesive bonding, resulting in lower assembly costs. The chassis is made up of five parts - front and rear bulkheads, floor pan and left and right body side panels - bonded to a central aluminium spine. The composite parts are manufactured as a sandwich structure with a core material made from hollow tubes of recycled polycarbonate. The laminate either side of this core uses a single ply of recycled chopped carbon fibre in the form of a multiaxial mat, and a resin blend of polyurethane and RTM-grade epoxy. For the 1.6 m x 1.7 m chassis floor, two carbon fibre multiaxial reinforcements produced by Hexcel Reinforcements UK (formerly FORMAX) are also specified. Should the vehicle be involved in a crash, these reinforcements are engineered to spread the seat belt pull-out load over the largest possible area, ensuring the metal seat belt inserts positioned under the floor remain in place.
Open the catalog to page 1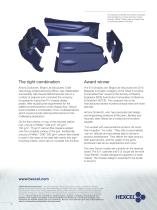
The chassis comprises five carbon composite parts bonded to a central aluminium spine. Hexcel’s HiMax™ fabrics play an integral role in reinforcing areas of the floor. The right combination Antony Dodworth, Bright Lite Structures’ Chief Technology & Manufacturing Officer, has collaborated successfully with Hexcel Reinforcements UK on a number of projects and contacted the company for guidance during the E10 chassis design phase. After studying the requirements for the additional reinforcement of the chassis floor, Hexcel recommended a combination of two multiaxial fabrics which would...
Open the catalog to page 2All HEXCEL catalogs and technical brochures
-
HexPly® M79
6 Pages
-
HexPly® M78
4 Pages
-
HexTow® HM63
2 Pages
-
HiMax™ glass multiaxials
8 Pages
-
HexForce® Reinforcements
99 Pages
-
HexTow® Carbon Fiber
8 Pages
-
HexcelinAerospace
8 Pages
-
HexShield_ProductFlyer
2 Pages
-
HiTape
4 Pages
-
Rail
5 Pages
-
wintersports
6 Pages
-
Wind_Turbine_Blades
12 Pages
-
AutomotiveBrochure
4 Pages
-
Industrial
16 Pages
-
Aerospace
16 Pages
-
HiTape®
4 Pages
-
HexWeb® Acousti-CAP®
4 Pages
-
Aerospace Selector Guide
16 Pages
-
HexTow® Chopped Fiber
2 Pages