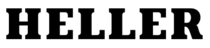

Catalog excerpts
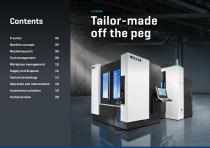
Operation and maintenance 16 Automation solutions 18
Open the catalog to page 2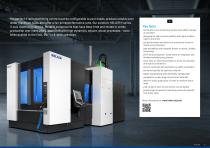
The perfect 4-axis machining centre must be configurable to your needs, produce reliably even under maximum loads and offer a fair price/performance ratio. Our solution: HELLER H series 4-axis machining centres. Reliable components that have been tried and tested in series production over many years, combined with high dynamics, ensure robust processes – even when pushed to the limit, 24/7 in 3-shift operation. Key facts _horizontal 4-axis machining centres with pallet changer as standard _designed for high process stability and highly resilient right to the limits _top performance and...
Open the catalog to page 3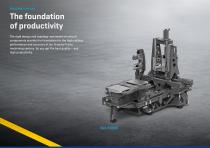
Machine concept The foundation of productivity The rigid design and topology-optimised structural components provide the foundation for the high cutting performance and accuracy of our H series 4 axis machining centres. So you get the best quality – and high productivity.
Open the catalog to page 4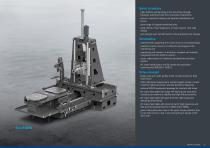
Basic structure _high stability and damping in the force flow through topology-optimised cast iron structural components _thermo-symmetric design and optimum distribution of forces _wide range of rugged machining units _wide choice of tool magazines, in chain-type or rack-type design _tool changer with two NC axes for fast automatic tool change Kinematics _machine bed supporting the X and Z axes in cross bed design _machine column moves in X-direction and supports the machining unit _machining unit moves in Y-direction, compact and robustly integrated into the machine column...
Open the catalog to page 5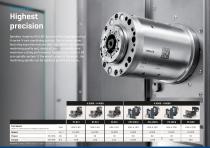
Machining units Highest precision Spindles 'made by HELLER' are one of the highlights of our H series 4-axis machining centres. Our in-house manufacturing expertise ensures that they deliver the highest machining quality and, above all, process stability and maximum cutting performance. Special plus: the HELLER zero spindle system. If the worst comes to the worst, the machining spindle can be replaced quickly and easily.
Open the catalog to page 6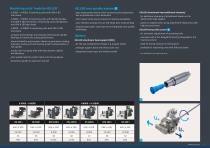
Machining units 'made by HELLER' _H 2000 - H 4000: 3 machining units with HSK-A 63 tool shank _H 5000 - H 6000: 3 machining units with INLINE spindles and HSK-A 100 tool shank, 3 machining units with gearbox and HSK-A 100 tool shank _H 8000 - H 16000: 5 machining units with HSK-A 100 tool shank _compact overall design and robustly dimensioned spindle bearings for maximum cutting performance _thermal stability and precision thanks to permanent cooling: precision cooling unit and thermal growth compensation of the spindle _sturdy cast iron guide slide with high dynamic rigidity and damping...
Open the catalog to page 7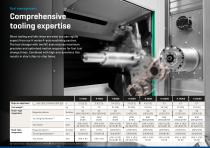
Tool management Comprehensive tooling expertise Short tooling and idle times are what you can rightly expect from our H series 4-axis machining centres. The tool changer with two NC axes ensures maximum precision and optimised motion sequences for fast tool change times. Combined with high axis dynamics this results in short chip-to-chip times. kg Chip-to-chip time1! t23 | VDI 2852 | POWER [SPEED] Tool weight2 ( ) = Opti onal values 1) Applies to Siemens SINUMERIK 2) Consider total load capacity 3) With free adjacent places
Open the catalog to page 8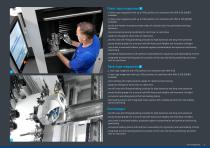
Chain-type magazines _4 chain-type magazines with up to 240 positions for machines with HSK-A 63 (SK/BT) available _3 chain-type magazines with up to 150 positions for machines with HSK-A 100 (SK/BT) available _sturdy tool holders mounted on both sides of a double chain for optimised traversing dynamics _tool provisioning during machining for short tool-to-tool times _rapid tool change for short chip-to-chip times _two NC axes with lifting/swivelling principle for high dynamics and long-term precision _sturdy double gripper for a secure hold with heavy tool weights and moments...
Open the catalog to page 9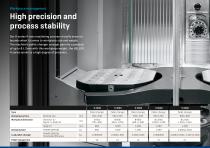
Workpiece management High precision and process stability Our H series 4-axis machining centres virtually know no bounds when it comes to workpiece size and weight. The machine’s pallet changer concept permits a payload of up to 8 t. Even with this workpiece weight, the HELLER H series works to a high degree of precision. Pallet changer Pallet changer Pallet changer Pallet changer Clamping surface Nominal size Workpiece dimension Diameter D / Depth T x Width W Clamping load POWER ( SPEED ) Load pallet changer POWER (SPEED) Total/load difference
Open the catalog to page 10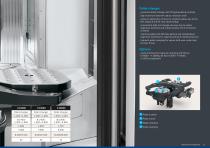
Pallet changer _automatic pallet changer with lifting/swivelling principle _high maximum load with robust, hydraulic drive _optimum application of force to machine pallets due to the fork shape of the lift-and-swivel bridge consistently high tool change accuracy due to robust alignment elements and extensive blow-off of functional surfaces _machine pallets with DIN hole pattern and standardised alignment elements for rapid mounting of clamping fixtures _hydraulic pallet clamping for secure hold, even under high process forces Options _media interface for hydraulic clamping with 60 bar (H...
Open the catalog to page 11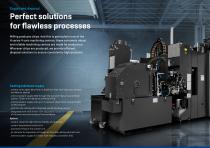
Perfect solutions for flawless processes Milling produces chips. And this is particularly true of the H series 4-axis machining centres: these extremely robust and reliable machining centres are made for production. Wherever chips are produced, we provide efficient disposal solutions to ensure consistently high precision. Cooling lubricant supply _coolant units: paper band filter or backflush filter with high tank volumes available as options _internal coolant supply (IKZ) through the tool with high pressure 50 bar (option: 70 bar with frequency converter (FU)) _internal coolant supply...
Open the catalog to page 12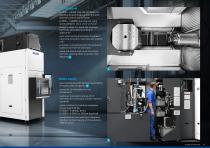
Chip disposal _H 2000 – H 6000: free chip fall below the spindle and quick disposal from the work area with central chip conveyor _H 8000 – H 16000: chip disposal using spiral conveyors and a cross-conveyor _design: scraper or hinged belt conveyor (optional), selectable according to application _work area flushing and shower to support rapid chip removal in machines with coolant units _extraction unit (optional) for the removal of coolant mist from the work area _steep side panels and concertina covers with self-cleaning effect to prevent chip deposits 1 Media supply _easy...
Open the catalog to page 13All Heller Machine Tools Ltd catalogs and technical brochures
-
5-axis machining centres F/C
28 Pages
-
5-axis machining centres HF
28 Pages