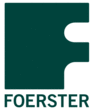
Catalog excerpts
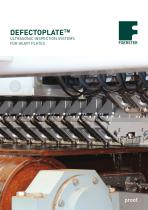
DEFECTOPLATE™ ULTRASONIC INSPECTION SYSTEMS FOR HEAVY PLATES
Open the catalog to page 1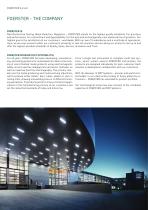
FOERSTER - THE COMPANY FOERSTER IS Non-Destructive Testing, Metal Detection, Magnetics – FOERSTER stands for the highest quality standards. For precision and performance. For commitment and dependability. For the best and technologically most advanced line of products. Our highest goal is the satisfaction of our customers – worldwide. With our own 10 subsidiaries and a multitude of representatives, we are ever-present within our customers’ proximity in over 60 countries and are doing our utmost to live up to and offer the highest possible standards of Quality, Value, Service, Innovation and...
Open the catalog to page 2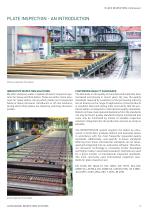
PLATE INSPECTION ■ Ultrasonic PLATE INSPECTION - AN INTRODUCTION Off-line inspection from above INNOVATIVE INSPECTION SOLUTIONS We offer stationary water-coupled ultrasonic inspection systems for heavy and thick plates. These are either inline solutions for heavy plates, during which plates are transported below or above ultrasonic transducers or off-line solutions, during which thick plates are tested by scanning ultrasonic probes. CUSTOMIZED QUALITY ASSURANCE The demands on the quality of manufactured materials have increased enormously in recent years. By now, the quality standards...
Open the catalog to page 3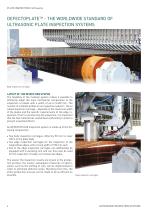
PLATE INSPECTION ■ Ultrasonic Edge inspection carriages LAYOUT OF THE INSPECTION SYSTEM The flexibility of the modular system makes it possible to efficiently adapt the main mechanical components to the inspection of plates with a width of up to 5.400 mm. The number of installed probes on an inspection subunit - the so called inspection carriage - depends on the maximum width of the plates and the specific requirements of the edge inspection. Prior to commencing the inspection, it is important that the test material has cooled down sufficiently in order to prevent unwanted effects. An...
Open the catalog to page 4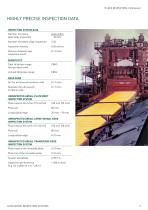
PLATE INSPECTION ■ Ultrasonic INSPECTION SYSTEM DATA_ Number of probes, plate width plate body inspection 50 mm Number of probes, edge inspection 2 (4) Inspection velocity < 60 m/min Distance between two < 1.0 mm inspection shots SENSITIVITY Total thickness range FBH3 (except dead zone) Limited thickness range FBH2 DEAD ZONE On the ultrasound incidence side < 1.5 mm Opposite the ultrasound < 1.5 mm incidence side UNINSPECTED AREAS, PLATE BODY INSPECTION SYSTEM Plate head at 60 m/min (15 m/min) 150 mm (70 mm) UNINSPECTED AREAS, LONGITUDINAL EDGE INSPECTION...
Open the catalog to page 5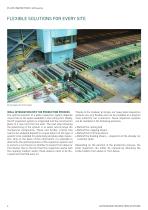
PLATE INSPECTION ■ Ultrasonic FLEXIBLE SOLUTIONS FOR EVERY SITE Inline inspection from below IDEAL INTEGRATION INTO THE PRODUCTION PROCESS The optimal position of a plate inspection system depends most of all on the space available in the rolling mill. Ideally, the UT inspection system is integrated into the construction plans of a new mill from the start. The next step following the positioning of the system is to select and arrange the mechanical components. These and further criteria that need to be analyzed depend to a large extent on the type of system to be installed for plate body...
Open the catalog to page 6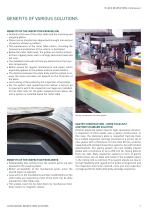
PLATE INSPECTION ■ Ultrasonic BENEFITS OF VARIOUS SOLUTIONS BENEFITS OF THE INSPECTION FROM BELOW ■■ Unobstructed view of the roller table and the incoming and outgoing plates. ■■ Plates can be transferred, aligned and brought into and out of position without a problem. ■■ The maintenance of the roller table rollers, including the removal and installation of the rollers, is facilitated. ■■ Below the roller table level, the probes are better protected from rippled plates with a strongly deformed head and tail zone. ■■ The installed crane will not face any obstructions from system components....
Open the catalog to page 7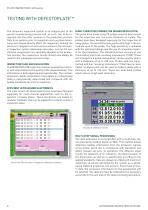
PLATE INSPECTION ■ Ultrasonic TESTING WITH DEFECTOPLATE TM The ultrasonic inspection system is an integral part of the overall manufacturing process and, as such, has to be integrated into the other systems in the production process. Data from systems prior to inspection such as plate dimensions and shapes directly affect the inspection, making the electronic integration of and communication to the ultrasonic inspection system absolutely necessary. Just as the mechanical components are optimally adjusted to the production process, the inspections results should also ideally be used for the...
Open the catalog to page 8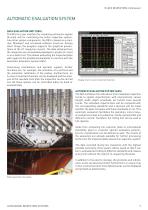
PLATE INSPECTION ■ Ultrasonic AUTOMATIC EVALUATION SYSTEM DATA EVALUATION UNIT (DEU) The DEU is a user interface for visualizing ultrasonic signals (A-scan) and for controlling the entire inspection system. Like other system components, the DEU is based on a modular, Windows® and net-based software structure. Among other things, the program supports the graphical presentation of the UT inspection results. The data obtained from the inspection are immediately displayed in graphs (C-scan) or as a defect list. This allows evaluating the inspected plate with regard to the predefined standards...
Open the catalog to page 9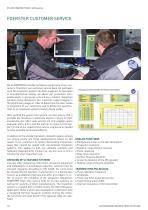
PLATE INSPECTION ■ Ultrasonic We at FOERSTER consider ourselves as partners of our customers. Therefore, our customer service does not just begin once the inspection system has been supplied. As specialist in non-destructive testing, we advise our customers comprehensively in all issues concerning a modern inspection solution using ultrasound. Our customer support begins in the preliminary stages in order to determine the exact needs of inspection of our customers and to define the specifications of an inspection system meeting these needs. After putting the system into service, we also...
Open the catalog to page 10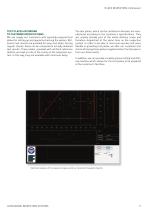
PLATE INSPECTION ■ Ultrasonic TEST PLATES ACCORDING TO CUSTOMER SPECIFICATIONS We can supply our customers with specially prepared test plates for setting up and regularly checking the system. Reference test results are provided for every test plate. During regular checks, these can be compared to actually obtained test results. These plates, provided with artificial reference defects, are kept on-site in the vicinity of the inspection system. In this way, they are available with minimum delay. The test plates, which can be certified on demand, are manufactured according to the customer’s...
Open the catalog to page 11All Foerster Instruments catalogs and technical brochures
-
DATAL OAD2 SOFTWARE
2 Pages
-
DEFECTOVISION ® IR
8 Pages
-
DEFECTOMAT ®
16 Pages