
Catalog excerpts
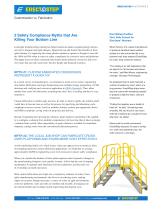
3 Safety Compliance Myths that Are Killing Your Bottom Line ErectAStep Enables Fast, Safe Access for Shurtape ® Workers Lean/agile manufacturing training has helped numerous plants respond quickly and proactively to frequent and rapid changes. Despite the top and bottom line benefits of lean/ agile training, it’s surprising how many plants continue to operate as though it were still the 1980s and 90s when it comes to safety compliance for crossover stairs and platforms. This paper uncovers three commonly held myths about industrial crossovers and crossover stairs that not only waste time, but also people and financial resources. When Hickory, N.C.-based manufacturer of pressure-sensitive tapes needed access to a silo surrounded by a containment wall, they selected ErectAStep for a fast, easy crossover solution. MYTH #1: CUSTOM FABRICATED CROSSOVERS REPRESENT A QUICK FIX In a recent survey of manufacturers, we estimated as much as two weeks’ engineering time before fabrication can begin. Engineering time includes design, preparation of CAD drawings and verifying each crossover application to OSHA Standards. Then, allow another four weeks for fabrication, assuming they don’t have a backlog and they’re very responsive. Custom fabrication is neither agile nor lean. In order to achieve agility, the solution itself would have to become lean as well as the process for specifying and obtaining a safe, compliant crossover system. Look for modular, turnkey systems pre-engineered, drawn and OSHA compliant, saving weeks in prep time and delivery. Instead of spending time drawing the solutions, plant engineers should have the capability to configure a solution from modular components in far less time than it takes to design a solution from scratch. More importantly, an agile solution is available for immediate shipment, cutting weeks from the conventional fabrication process. MYTH #2: THE LOCAL JOB SHOP CAN FABRICATE CROSSOVER PLATFORMS AND STAIRS MORE COST EFFECTIVELY Avoid considering initial cost, which at face value may appear to be economical. After investigating numerous custom fabrication applications, we found that on average, approximately $4,000 in engineering costs were necessary to ensure safety compliance. When you consider the number of times plant engineers must respond to changes in the manufacturing footprint, costs quickly escalate. Add to that the cost of ongoing maintenance for painted steel fabricated crossover platforms, and the total cost of ownership can really skyrocket. Most custom fabrications are single use or temporary solutions. In today’s lean, agile manufacturing environments, the focus is on reducing waste, making single use systems, though necessary, a source of waste. In agile environments, crossover platforms, stairs and rails are modular and reusable, leveraging your investment further and avoiding wasted engineering and disposal costs. toll free 1.888.878.1839 internationally +1.843.485.0630 or online at erectastep.com “The catalog is so self explanatory that we spec’d it in 30 minutes and placed the order,” said Matt Moore, engineering manager, Shurtape Technologies. He explained that his team had built a number of ladders by hand, which is a long process. ErectAStep ships same day and comes with everything needed to properly install the stairs, rails and crossovers. “Putting this together was a breath of fresh air,” he said. “Everything went smoothly. We had it built in two hours and had it ready to go a couple of hours after that,” he added. Moore said he would recommend ErectAStep because it’s easy to configure, order and assemble; plus, the orde
Open the catalog to page 1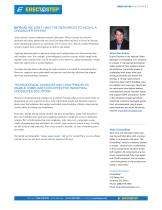
MYTH #3: WE DON’T HAVE THE RESOURCES TO INSTALL A CROSSOVER SYSTEM A lean process ensures optimum resource allocation. When it comes to crossover platforms and stairs, plants that use a local job shop often find they’re forced to allocate more engineering resources at a premium cost. In some cases, heavily welded fabricated systems require more costly logistics to deliver and install. Applying lean principles to upstream design and configuration saves downstream time and contains costs. For example, a preconfigured crossover system, which simply bolts together with common tools, can be...
Open the catalog to page 2All ErectaStep catalogs and technical brochures
-
Tri-fold Brochure
6 Pages
-
Portable and Adjustable
2 Pages
-
DIMENSIONAL SPEC SHEET
6 Pages
-
ErectaStep Catalog
6 Pages
-
erectastep_comp_specs
5 Pages
-
erectastep_catalog
68 Pages