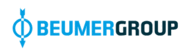

Catalog excerpts
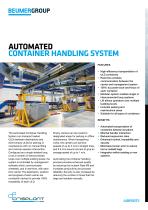
Automated Container Handling System FEATURES • High-efficiency transportation of ULD containers • Real-time wireless communication between the carrier and management system • 100% accurate track-and-trace of each container • Modular system enables single or interconnected loop systems • Lift allows operation over multiple building levels • Includes parking and maintenance areas • Suitable for all types of containers BENEFITS The Automated Container Handling System can transport loaded ULDs between destinations and divert empty ULDs for parking or maintenance with no manual lifting and minimal operator intervention. Configured as a single isolated loop, or as a number of interconnected loops over multiple building levels, the system is controlled by management software which communicates wirelessly, and in real-time, with each ULD carrier. The destination, position and progress of each carrier are constantly tracked to provide 100% traceability of each ULD. Empty carriers can be routed to designated areas for parking or offline maintenance. When transporting ULDs, the carriers can achieve speeds of up to 2 m/s in straight lines, and 0.5 m/s around corners to give an average speed of up to 1 m/s. • Automated transportation of containers between locations • Minimal handler interaction • Reduced ergonomic risks • Enhanced control, traceability and security • Minimises human error to reduce lost or mislaid bags • Integration within existing or new systems Automating the container handling process provides enhanced quality by reducing the Incident Rate (IR) and increases productivity and process reliability. Security is also increased by reducing the number of times that the bags are hand
Open the catalog to page 1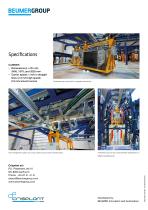
Specifications Carrier • Dimensions (L x W x H): 3400, 1570, and 2020 mm • Carrier speed: 1 m/s in straight lines or 2 m/s high speed; 0.5 m/s around curves Containers are moved with no operator intervention The management system can route carriers around interconnected loops A lift allows ULDs to be moved between destinations on different building levels Developed by: BEUMER Innovation and Automation Crisplant a/s P.O. Pedersens Vej 10 DK-8200 Aarhus N Phone: +45 87 41 41 41 airport@beumergroup.com www.beumergroup.co
Open the catalog to page 2All CRISPLANT - BEUMER GROUP catalogs and technical brochures
-
BHS
6 Pages
-
CrisBelt
2 Pages
-
CRISCHECK ®
2 Pages
-
DATA ANALYTICS
2 Pages
-
CRISSTORE®
2 Pages
-
BAGGAGE LOADER
2 Pages
-
BEUMER fillpac® FFS
2 Pages
-
BEUMER Group Profile
8 Pages
-
DISTRIBUTION CENTRE
4 Pages
-
AUTOPAC
4 Pages
-
BEUMER BELT BUCKET ELEVATOR
2 Pages
-
BEUMER LS-4000econ
4 Pages
-
BEUMER Baggage Loader
2 Pages
-
BEUMER CrisBelt
2 Pages
-
BEUMER Identification Unit
2 Pages
-
BEUMER CrisClaim®
2 Pages
-
BEUMER CrisBag®
4 Pages
-
BEUMER LS-4000E for Airports
4 Pages
-
BEUMER Airport
8 Pages
-
BEUMER autover®
4 Pages
-
BEUMER Baggage Unloader
2 Pages
-
BEUMER CrisCheck
2 Pages
-
BEUMER BagLog 11
8 Pages
-
BEUMER Remote Encoding
2 Pages
-
BEUMER TrayDeck
2 Pages
-
BEUMER Visualisation
2 Pages
-
Identification Unit
2 Pages
-
CrisClaim®
2 Pages
-
CrisBag®
4 Pages
-
autover®
4 Pages
-
Baggage Unloader
2 Pages
-
CrisCheck
2 Pages
-
LS-4000CB Cross-Belt Sorter
4 Pages
-
Management Information
2 Pages
-
Remote Encoding
2 Pages
-
TrayDeck
2 Pages
-
Visualisation
2 Pages
-
LS-4000econ
4 Pages
-
Baggage Manipulator
2 Pages
-
Baggage Lifting Table
2 Pages
-
Automated Container Unloader
2 Pages
-
Bag Forklift
2 Pages
-
AIRPORT SOFTWARE SUITE
6 Pages
-
EARLY BAGGAGE STORAGE
2 Pages
-
INDEPENDENT CARRIER SYSTEM
4 Pages
-
CHECK-IN_CONVEYORS
2 Pages
-
BAGGAGE handling
8 Pages