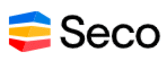
Extraits du catalogue
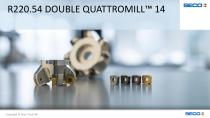
Copyright © 2018 Seco Tools AB Copyright © Seco Tools A
Ouvrir le catalogue en page 1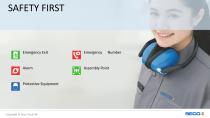
SAFETY FIRST Emergency Exit Assembly Point Protective Equipment Copyright © Seco Tools AB
Ouvrir le catalogue en page 2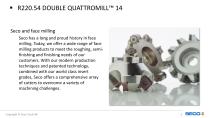
▪ R220.54 DOUBLE QUATTROMILL™ 14 Seco and face milling Seco has a long and proud history in face milling. Today, we offer a wide range of face milling products to meet the roughing, semifinishing and finishing needs of our customers. With our modern production techniques and patented technology, combined with our world class insert grades, Seco offers a comprehensive array of cutters to overcome a variety of machining challenges. Copyright © Seco Tools AB
Ouvrir le catalogue en page 3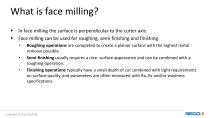
What is face milling? ■ In face milling the surface is perpendicular to the cutter axis. ■ Face milling can be used for roughing, semi finishing and finishing. • Roughing operations are completed to create a plainer surface with the highest metal removal possible. • Semi-finishing usually requires a nice surface appearance and can be combined with a roughing operation. • Finishing operations typically have a small depth of cut combined with tight requirements on surface quality, and parameters are often measured with Ra, Rz and/or waviness specifications. Copyright © Seco Tools AB
Ouvrir le catalogue en page 4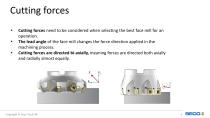
Copyright © Seco Tools AB 5
Ouvrir le catalogue en page 5
■ the most common variant used ■ Unstable machining operations and/or long overhangs ■ 68° lead angle ■ higher depths of cut with the same size I.C.< on the insert ■ beneficial at clamping fixture or other obstacle that cannot be avoided in the machining process. lead angle high depth of cut capabilities with smaller I.C. inserts. optimal when machining next to a side wall on a workpiece to avoid fixture clamping and other obstacles in the machining process. produces very high radial cutting forces (needs to be kept in mind in relation to fixture and machine stability) Copyright © Seco...
Ouvrir le catalogue en page 6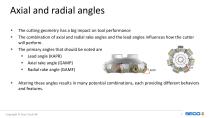
■ The cutting geometry has a big impact on tool performance ■ The combination of axial and radial rake angles and the lead angles influences how the cutter will perform. ■ The primary angles that should be noted are ■ Lead angle (KAPR) ■ Axial rake angle (GAMP) ■ Radial rake angle (GAMF) ■ Altering these angles results in many potential combinations, each providing different behaviors and features. Copyright © Seco Tools AB
Ouvrir le catalogue en page 7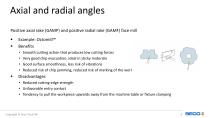
Positive axial rake (GAMP) and positive radial rake (GAMF) face mill ■ Example: Octomill™ ■ Benefits • Smooth cutting action that produces low cutting forces • Very good chip évacuation, idéal in sticky materials • Good surface smoothness, less risk of vibrations • Reduced risk of chip jamming, reduced risk of marking of the worl ■ Disadvantages • Reduced cutting edge strength • Unfavorable entry contact • Tendency to pull the workpiece upwards away from the machine table or fixture clamping Copyright © Seco Tools AB
Ouvrir le catalogue en page 8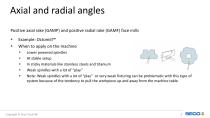
Positive axial rake (GAMP) and positive radial rake (GAMF) face mills ■ When to apply on the machine ■ Lower powered spindles ■ At stable setup ■ In sticky materials like stainless steels and titanium ■ Weak spindles with a lot of "play" Note: Weak spindles with a lot of "play" or very weak fixturing can be problematic with this type of system because of the tendency to pull the workpiece up and away from the machine table. Copyright © Seco Tools AB
Ouvrir le catalogue en page 9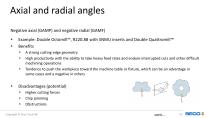
Négative axial (GAMP) and négative radial (GAMF) ■ Example: Double Octomill™, R220.88 with SNMU inserts and Double Quattromill™ ■ Benefits ■ A strong cutting edge geometry ■ High productivity with the ability to take heavy feed rates and endure interrupted cuts and other difficult machining operations ■ Tendency to push the workpiece toward the machine table or fixture, which can be an advantage in some cases and a negative in others ■ Disadvantages (potential) ■ Higher cutting forces ■ Chip jamming ■ Obstructions Copyright © Seco Tools AB
Ouvrir le catalogue en page 10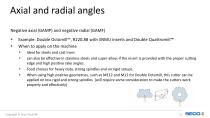
Axial and radial angles Negative axial (GAMP) and negative radial (GAMF) ▪ ▪ Example: Double Octomill™, R220.88 with SNMU inserts and Double Quattromill™ When to apply on the machine ▪ ▪ ▪ ▪ Ideal for steels and cast irons can also be effective in stainless steels and super alloys if the insert is provided with the proper cutting edge and high positive rake angles. Food choices for heavy duty, strong spindles and on rigid setups. When using high positive geometries, such as ME12 and M12 for Double Octomill, this cutter can be applied on less rigid and strong spindles (will require some...
Ouvrir le catalogue en page 11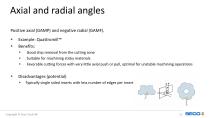
Positive axial (GAMP) and négative radial (GAMF). ■ Example: Quattromill™ ■ Benefits: ■ Good chip removal from the cutting zone ■ Suitable for machining sticky materials ■ Favorable cutting forces with very little axial push or pull, optimal for unstable machining operations Disadvantages (potential) ■ Typically single sided inserts with less number of edges per insert Copyright © Seco Tools AB
Ouvrir le catalogue en page 12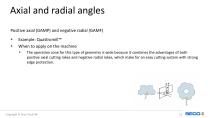
■ The operation zone for this type of geometry is wide because it combines the advantages of both positive axial cutting rakes and negative radial rakes, which make for an easy cutting system with strong edge protection. Copyright © Seco Tools AB
Ouvrir le catalogue en page 13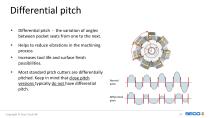
■ Differential pitch - the variation of angles between pocket seats from one to the next. ■ Helps to reduce vibrations in the machining process ■ Increases tool life and surface finish possibilities. ■ Most standard pitch cutters are differentially pitched. Keep in mind that close pitch versions typically do not have differential pitch. Copyright © Seco Tools AB 14 SECO
Ouvrir le catalogue en page 14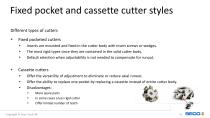
Different types of cutters ■ Fixed pocketed cutters ■ Inserts are mounted and fixed in the cutter body with insert screws or wedges. ■ The most rigid types since they are contained in the solid cutter body. ■ Default selection when adjustability is not needed to compensate for runout. ■ Cassette cutters ■ Offer the versatility of adjustment to eliminate or reduce axial runout. Offer the ability to replace one pocket by replacing a cassette instead of entire cutter body. ■ Disadvantages: ■ More spare parts ■ In some cases a less rigid cutter ■ Offer limited number of teeth Copyright © Seco...
Ouvrir le catalogue en page 15Tous les catalogues et fiches techniques (PDF) SECO TOOLS
-
SECO NEWS
310 Pages
-
Solid End Mills.pdf
641 Pages
-
Indexable Milling Catalog.pdf
856 Pages
-
Taper-Face Toolholders.pdf
23 Pages
-
GL25-HEADS RANGE EXPANSION
13 Pages
-
SECO NEWS SUMMARY 2019.1
9 Pages
-
DOUBLE OCTOMILL™
2 Pages
-
PRODUCT SUMMARY
2 Pages
-
SECO NEWS SUMMARY 2018.1
14 Pages
-
POZVÁNKA ZD KOVOSVIT
1 Pages
-
Machinability_poster
1 Pages
-
SQUARE T4
2 Pages
-
SECO Product summary
2 Pages
-
DURATOMICTM
16 Pages
-
QUATTROMILL-AL™
2 Pages
Catalogues archivés
-
CATALOGUE ET GUIDE TECHNIQUE 2018
407 Pages
-
Fraise-disque 335.25
2 Pages
-
DISC MILLING
36 Pages